Duration: 12 months
The additive manufacture (AM) of nickel superalloy components increases the opportunities for light-weighting, geometric freedom and rapid prototyping, making it ideal for space applications. Current standards for AM parts in space applications (ECSS-Q-ST-70-80-C and AMS7031) do not allow for the reuse of powder without first checking the powder meets its specification after each reuse step. This adds time and cost, especially in industrial-scale machines such as the Renishaw RenAM 500Q, where powder is reused internally and returned to the hopper after every build. However, there are no studies to date that evaluate the impact of reuse in these state-of-the-art machines. As the space industry moves into industrial production of flight hardware, there is a need for more efficiency (e.g. faster build, less raw material wastage) whilst ensuring high quality products. The proposed work intends to define safe limits for powder reuse in systems using internal continuous (closed-loop) reuse within the machine, applicable to all closed loop reuse systems. Determining if there is powder stratification in the hopper after internal reuse will be important, and sufficient mixing to homogenize the powder should be ensured. ABD®-900AM has been chosen as the material for this work. As a high-temperature nickel superalloy with the performance of Inconel 939, but the AM printability of Inconel 718, ABD®-900AM has a wide range of applications in the space sector and has been identified as the material of choice for components on current ESA missions. With the high cost of ABD®-900AM, increasing the number of reuse steps and optimising top-ups will decrease the cost of parts, as it will no longer be necessary to dispose of powder after a number of reuses. Lead times and environmental footprint of component production will also decrease, as the requirement for powder testing could be drastically reduced, enabling parts made using AM in this material for future ESA missions.
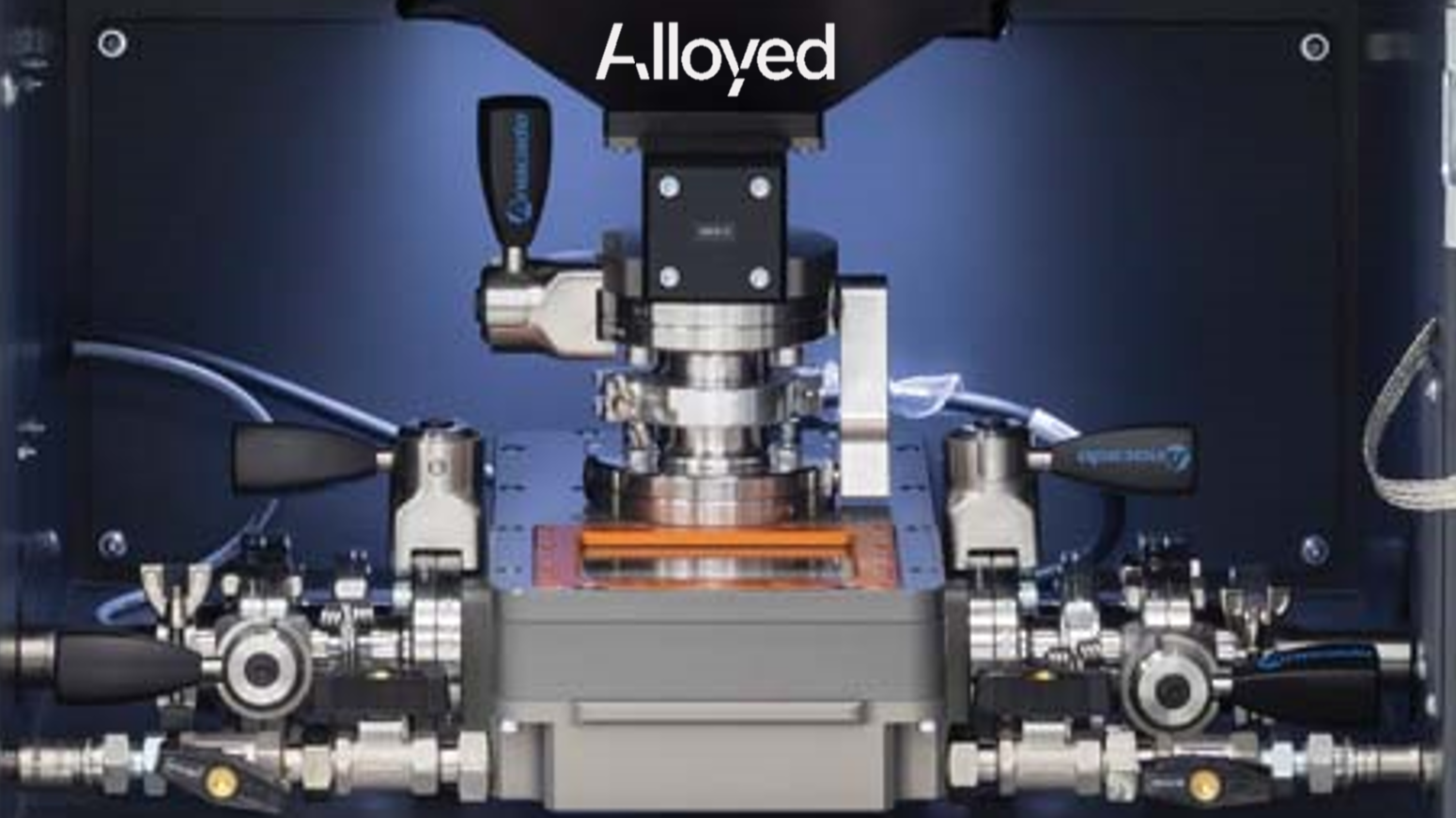