Duration: 18 months
The project's longer term goal is to demonstrate in-space manufacturing (ISM) and assembly (ISA) of large structures using carbon fiber tubular (CFRP) struts and customized photopolymer joints. By using a robotic arm, the tubes and joints are assembled into a higher order structure. With the vision to in-space assemble a parabolic antenna, this would result in a large number of different angled joint elements to approximate the parabolic surface. Therefore, it is an adequate solution to in-space manufacture these joint elements on demand rather than bringing them from Earth. Manufacturing these joints on demand makes them independent of high launch loads, increases packaging efficiency, requires no stock management for the individual joints and offer flexibility for in-situ adjustments . The project is based on the AMOCSIS project from the German Aerospace Center for the CFRP Struts and the ISA concept as well as form the ISM process of the Munich University of Applied Sciences (HM). So far, the CFRP struts deployment and the layer-by-layer printing process (3-axis, planar) could be demonstrated individually under laboratory conditions. However, to join the CFRP elements a customized 3D-printing process needs to be developed and tested to prove the overall concept. This is the objective of this proposed activity. The additional novelty is to support non-planar trajectories, to avoid dependencies on support structures and space debris. Photopolymer Extrusion can help achieve higher energy and packaging efficiency. Two different types of joints shall be identified and manufactured for this proof of concept. The influence of high vacuum during extrusion and curing will be investigated, to understand its effects on the process. ISA in combination with ISM will be key technologies for future spacecraft, as a solution for the demand of larger space structures that are needed to transmit high datarates, generate more electrical power or support space-based solar power.
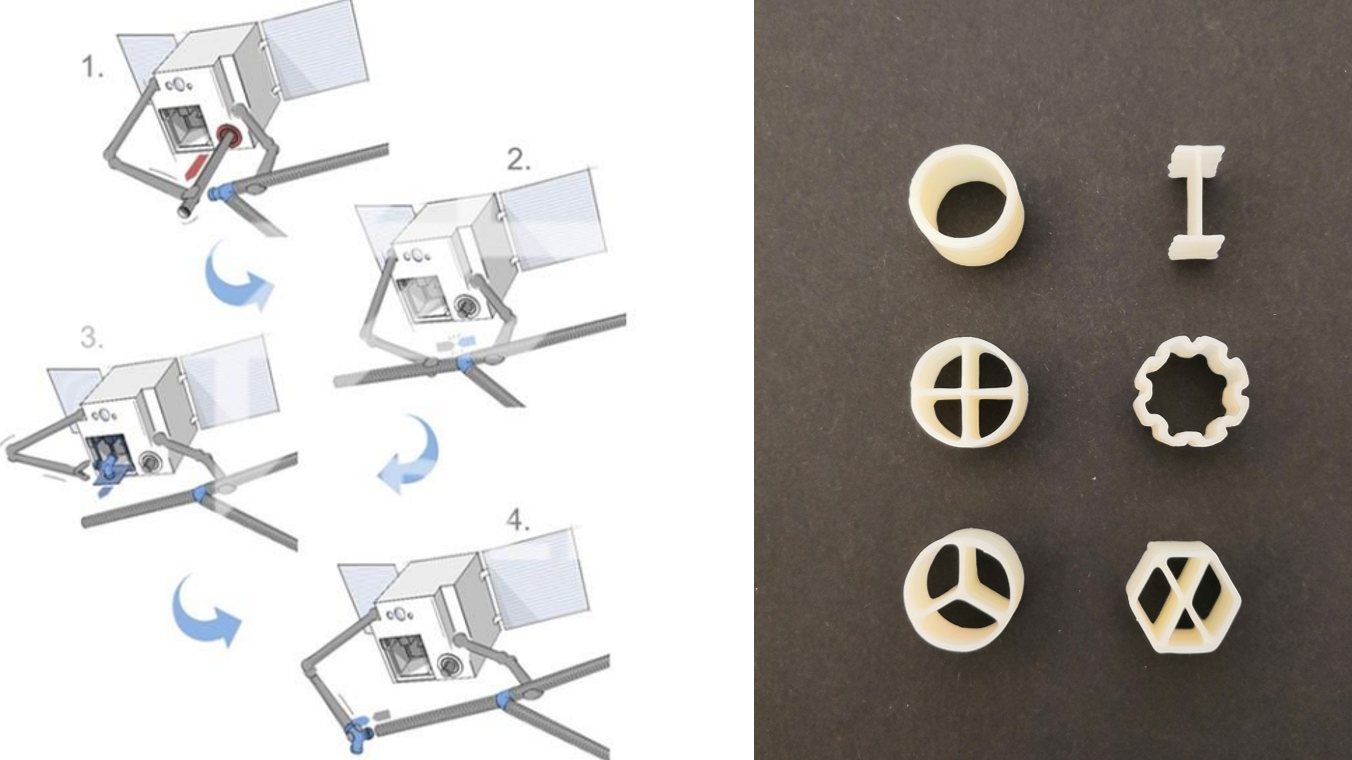