To ensure Europe's autonomous and cost-effective access to space while increasing the sustainability of launches, key technologies are being developed for future generation launchers. Within this context, landing leg systems are key enabler to rocket reusability and several technological demonstration programs have been recently initiated. Re-usability is key for both terrestrial operational scenarios and planned space exploration missions (Moon and Mars landing). Current reference design configuration for ‘Energy Absorption’ devices includes two sub-elements one of them being ‘crush cartridge assembly’ unit, whose function is activated whenever the off-nominal landing conditions are encountered. This unit features honeycomb-type crushable elements, assembled in a guiding system (to ensure proper crush directionality); the combined mass of this unit together with a hydraulic shock absorber unit exceeds 25% of the total allocated budget of the landing legs, with equivalent absorbed energy-to-mass ratio ranging from 1.3 kJ/kg to 1.8 kJ/kg. Emerging capability to fabricate lattice structures using additive manufacturing can ultimately lead to the replacement of the above-mentioned units with a quasi-monolithic unit, reducing the complexity of the system, its life cycle cost and the overall mass. Manufacturing of the additively manufactured lattice structures using shape memory alloys with reversible energy absorption capabilities will enable to produce efficient and re-usable smart shock absorbers. The objective of the project is analyze, evaluate and assess the technical feasibility of implementing a shape memory lattice structure component for high-efficiency re-usable shock absorption AM unit. To this end, we review the lattice structure designs and benchmark the predicted simulated performance with test data. The material of choice in this project is shape memory alloy NiTi, manufacturing of which we demonstrated in previous studies using laser powder bed fusion.
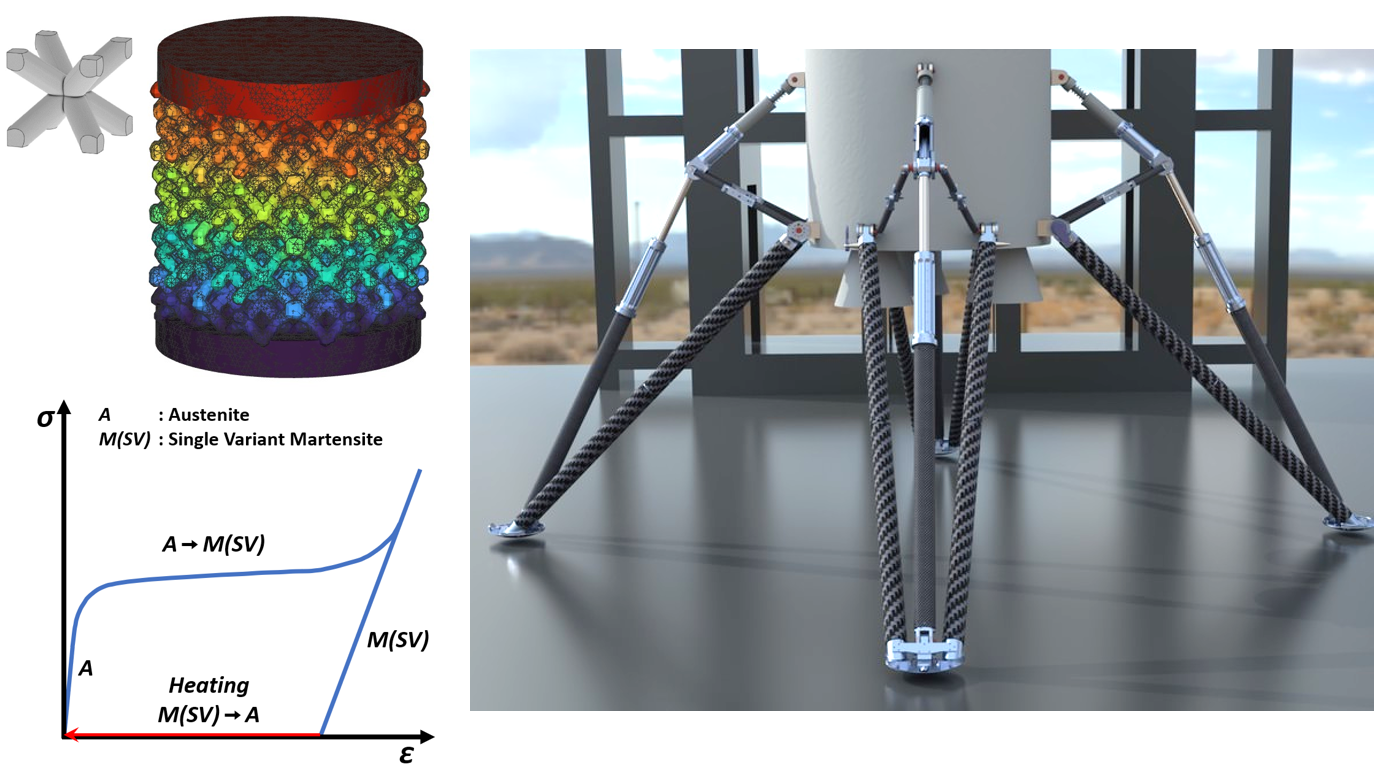