To date, the basic principles have been observed and the technology concept has been formulated, further validating the method in laboratory environments which represents a Technology Readiness Level of 4 (TRL 4). The method involves printing with an extruder head, and thermally debinding the main polymeric binder matrix by employing a low intensity diode laser, with a subsequent indirect induction sintering treatment. The results provided in the first manuscript indicate that local debinding on the same device is feasible, as the polymeric mass can be removed by focusing sufficient energy on the material, which layer by layer vaporizes the organic mass along the 3D volume of the shaped part. Using this approach, ablation of the main binder matrix has been achieved by concentrating electromagnetic energy on every layer of extruded material, with the ablated polymer escaping through the top surface open pores. Laser debinding is a promising route to decrease debinding times, as well as to reduce conventional thermal debinding defects such as bloating, blistering, and the generation of large internal voids. Additionally, the innovation allows to debind without the use of consumables, separate equipment, extended debinding cycles, nor toxic agents that pose significant threat to both environmental and user health.
Furthermore, the thesis has demonstrated in the second manuscript the capability of sintering MEAM metal parts with an efficient concentration of energy using indirect induction heating, rendering dense bodies in very short soaking time, as opposed to hours via the traditional approach. The microstructure and porosity content can be tailored depending on the heating times and rates. Within the third manuscript, the previously local laser debinded specimens were subjected to an indirect induction sintering treatment, further showcasing large densities albeit the reduced mechanical response compared to commercial 316L. Lastly, within the fourth manuscript, multi-material metal and ceramic samples were shaped, debinded, and sintered with this process, revealing the potential to build unprecedented functionally graded components. On the other hand, further investigations are necessary to adapt to new materials and increase the size of the built parts. Moreover, future trials shall focus on building high-quality multi-material metal-ceramic composities, experimenting on the most feasible combinations of materials using this process, as well as qualifying the process for space environments (i.e., microgravity, vacuum, thermal and radiation environment).
The general findings suggest that the combination of local debinding and sintering is feasible for MEAM metal and ceramic parts. This cumulative work unlocks unprecedented advancements that can be used in a future device in space, thereby providing the necessary groundwork to build advanced structures for future space missions.
The space industry is being revolutionized by the adoption of additive manufacturing (AM), providing unprecedented improvements in the performance of both spacecraft and launch vehicles. Highly complex and integrated subsystems can be manufactured on a single build, thus decreasing the overall mass, reducing single points of failure (i.e. risks), increasing the allowable payload mass and volume, and hence lowering costs. However, all S/C and rocket subsystems are comprised of more than one material, making it still complex today to adopt AM for highly integrated space hardware manufacturing - on Earth as well as in space. Multi-material AM machines were developed in the past [1], but these were focused on integrating a wide range of processes, rather than tailoring the technology for materials specific to space hardware. This research project aims to develop a multi-material AM machine capable of printing with space grade polymers (PEEK, ULTEM), ceramics (zirconia, alumina) and fully dense metals (stainless steel, copper), which will be used to manufacture highly integrated small satellite subsystems (e.g. structures, attitude control actuators, antennas, thermal control paths and mechanisms). A novel multi-material Fused Filament Fabrication (FFF) machine will be developed, whereby debinding and sintering of parts will be performed locally, during the manufacturing process, via a combination of different laser wavelengths and energies, allowing to take full advantage of multi-material AM. The advantage is that laser energy density can be changed in situ, thus enabling the combination of materials with different shrinkage and sintering behavior. At the end, the project will produce a 1U cubesat structure with integrated Fluid Dynamic Actuators [2]. The parts will be then qualified in a thermal-vacuum chamber, as well as for vibrations, and will be flown on the 1U TUPEX missions, and thus prove the feasibility of the machine for space hardware development.
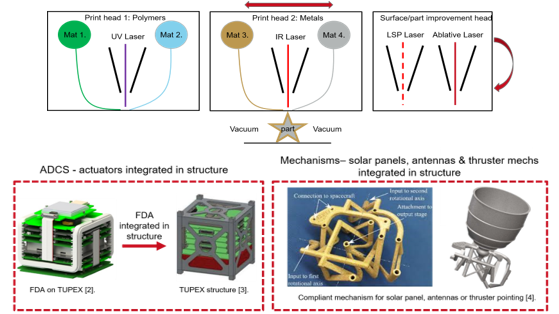