Duration: 18 months
Printed circuit board assemblies (PCBAs) must withstand various types of mechanical and thermal loads. For space applications, the ECSS standards define requirements for the verification of PCBAs assembled with the surface mount technology (SMT) and the through hole technology (THT). The technologies differ in PCBA design, manufacturing processes, and in the standardized test requirements, e.g., in 500 vs. 200 thermal cycles (-55°C/100°C) for SMT and THT assemblies, respectively. Whilst for SMT assemblies accelerated test models, e.g., the Norris-Landzberg model, are available to define accelerated test conditions for the simulation of field conditions, and there are tools available to model PCBAs, to simulate stress in the assembly and to predict the reliability, advanced tools and models for the THT have not been developed yet.
The requirement for THT assemblies was derived from empirical data based on the work of J. Halpin and based on data obtained at that time through testing and covering all failure types in an assembly. However, the relevance of this approach at present is questionable considering the evolution in the technology and material. More recently, parameters effecting the reliability of THT solder joints was investigated and compared with finite element (FE) analyses. However, FE analyses in these studies were limited to models of single solder joints. An interesting approach to simulate thermal cycling of THT assemblies used the sub-modelling approach with so-called global/local FE models. By combining this approach with an open-source FE solver and routines which can build FE models from PCBA manufacturing data automatically, reliability indicators, e.g., visco-plastic strain, could be calculated accurately and efficiently. These simulated indicators can improve the understanding of failure mechanisms in THT assemblies, provide confidence on the test regime currently applied, and to define new test regimes.
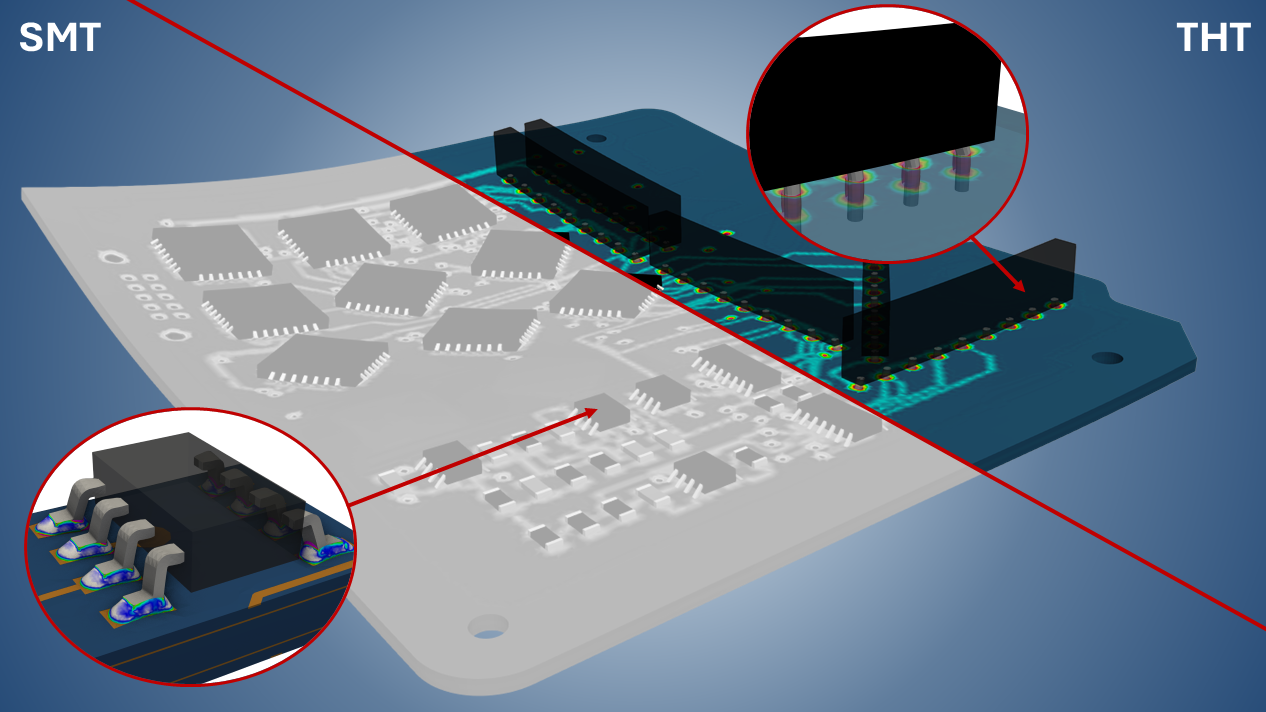