Aerospace industries need efficient, eco-friendly cooling devices. Solid-state cooling, which uses caloric materials that undergo adiabatic external field changes or entropy changes under isothermal external field application (e.g., magnetic fields or mechanical forces), is key to efficient, greenhouse gas-free refrigeration. However, current caloric devices face challenges such as fatigue resistance, large temperature spans, high specific cooling power, efficiency, and operational frequency. Traditional elastocaloric systems, based on uniaxial compression, are constrained by actuator needs, column buckling, and limited heat transfer surface area. Therefore, there is a need to develop new elastocaloric refrigeration systems with precise microstructure and topology to enhance the performance and durability of next-generation cooling concepts for space applications. We aim to propose new composites with unique elastocaloric effects and establish a platform for the fabrication of functionally graded materials into intricate architectures with localized elastocaloric value. For the first time, we will fabricate new multiscale superelastic materials with controlled composition using additive manufacturing (AM) that is beyond the state of the art by the arrangement of various lattice unit cells and node-reinforced structures. To achieve this goal, the objectives are: 1: To realize a new class of elastocaloric composite powder NiTi and NiMnTi based that will boost heat-pumping performance; 2: To develop the AM process, particularly laser powder bed fusion, that can manipulate the incorporation of caloric composite materials, resulting in functionally graded materials with site-specific properties; 3: To gain technical and fundamental knowledge on the parameters affecting the composition-performance-lifecycle characteristics of elastocaloric cooling materials; 4: Proof of concept 3D printing and demonstrating enhanced elastocaloric cooling materials.
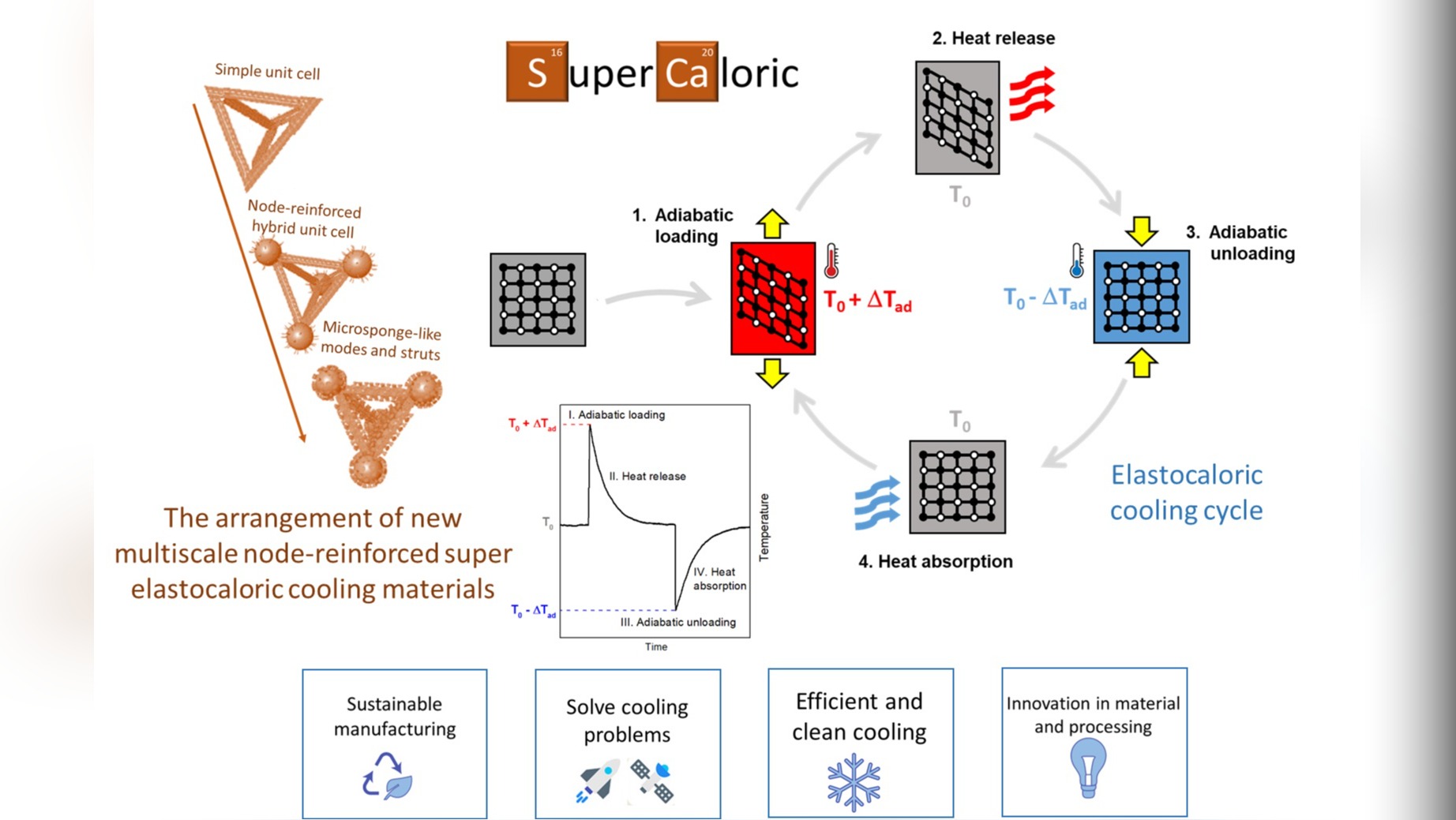