The reliability of each drive element is fundamental to space mechanism design. Where drive sub-systems must function in dusty environments, as for Lunar or Mars applications, gearboxes and bearings can be degraded, with lifetimes exponentially reduced if tribo-surfaces are exposed to abrasive media. Magnetic couplings can provide significant risk reduction for such applications, while offering an overdrive limiting capability tuned to allow normal operation while preventing excessive motor overheating/damage in extreme cases. By completely sealing the motor/gearbox from dust exposure, tribological limitations are avoided and the opportunity exists to develop a largely temperature independent drive element. Component design must be compatible with temperature effects and the system should be tolerant to drive-train compliance & phase lag behaviour. In dusty conditions, the coupling may also require lightly loaded sliding seals and/or labyrinths to limit dust ingress at the output shaft. Large magnetic gaps allow to improve dust tolerance versus much smaller motor gaps. The secondary effect of residual magnetic fields need to be assessed regarding attracting magnetic particles. This can be managed through design of the magnetic return to optimise containment of stray fields, by analysis/measurement to quantify field strength and gauge risk. Magnetic couplings in 3 distinct sizes will be designed and optimised to operate/survive in a realistic lunar environment. Use case specifications will be finalised as inputs to guide a sensitivity study & optimisation algorithm for 'micro, small & medium' classes, covering applications from instruments to shutters/port covers, drills & ISRU systems to rover drives. 2 breadboards of 1 coupling design will be built to demonstrate scalability vs an existing breadboard . Torque vs temperature will be correlated with analysis. Dust resilience will be verified by ambient dust injection testing & post-test inspection.
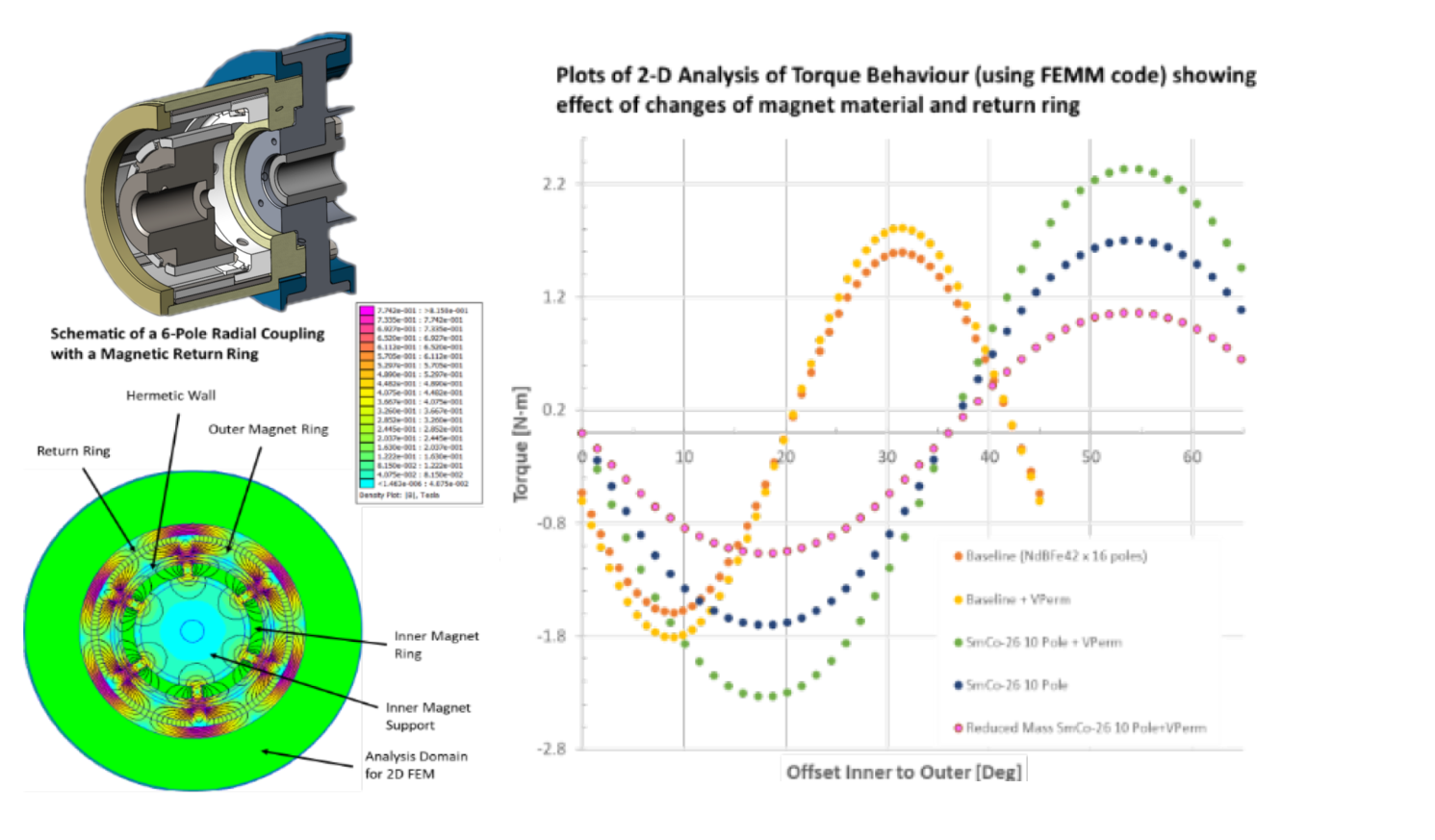