Free from wear, backlash, and lubrication, flexure-based guiding systems have become state-of-the-art solutions to develop long lifetime, high-precision, clean mechanisms operating in space. These notable advantages usually come with the drawback of high-quality factors which can lead to adverse effects when compliant mechanisms are submitted to launch vibrations and shocks, but also during operation, in the case of dynamic motions or in the presence of microvibrations. To tackle this challenge, CSEM developed and validated a patent pending concept of damped flexure blades based on additive manufacturing. The blades consist of a 3D printed sandwich of two thin, planar, parallel metallic lattice patterns with elastomer impregnated in-between in a 2nd step. The damping effect results from the energy dissipation occurring in the viscoelastic material as the blade deforms when the mechanism operates. These "Proof of Concept" blades were built and characterized under free oscillations in the framework of a Master Thesis. Compared with reference flexures, the damped flexures show quality factors Q reduced by a factor of 64. This reduction implies a damping action increased by a factor of 97 considering the viscous damping coefficient. The IP and scientific literature prior art research confirmed that there are currently no efficient solutions to overcome the above cited problems. Hence, this concept is to be seen as a breakthrough innovation for compliant mechanisms as it is significantly reducing their susceptibility to vibrations and shocks from large to small motion amplitudes. The damped flexure blade single element may also be seen as a building block to develop new topologies of spring dampers. Such dampers advantageously minimize exported vibrations of a variety of sources such as cryo-coolers or reaction wheels. Reversely the vibration susceptibility of systems such as optical benches could be reduced thanks to a decoupling from the surrounding environment.
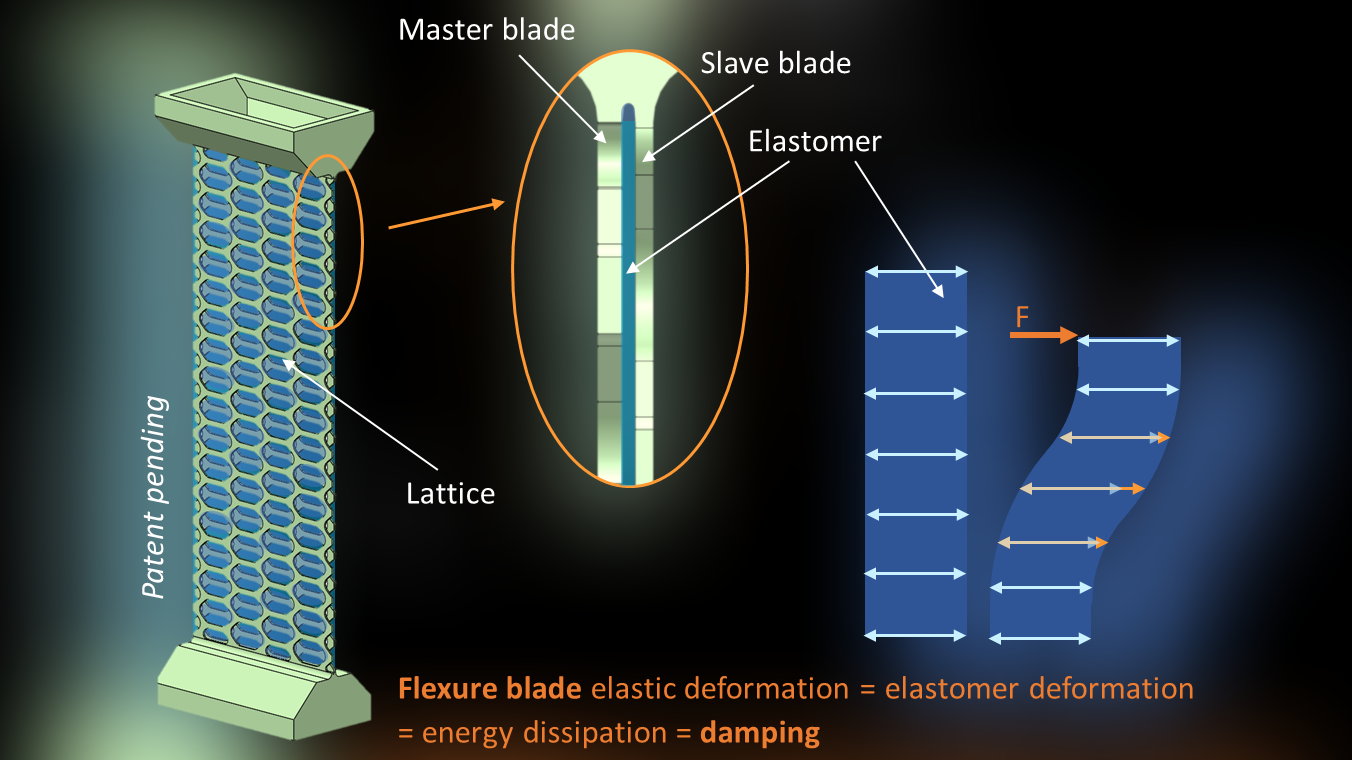