Spacecraft design can be described as a “balancing act” between mass reduction and reliability. For sandwich panels, one of the building blocks of modern spacecraft structures and sub-systems, lightweight materials such as aluminum and CFRP are commonly used.
Sandwich panels with embedded aluminum heatpipes are often used in S/C design answering the need of thermal control and structural performance. The use of CFRP materials is desirable to achieve lower mass, but currently is not considered technically feasible due to limitations arising from the CTE mismatch between the CFRP skins and the alloy of the heatpipes. Panels do not present any visible fault or damage, however when tested at low temperatures, premature failure (especially in potted inserts) has been observed, attributed to internal stresses in the skins.
The idea proposed aims to provide a lightweight solution to radically decrease these internal stresses and make CFRP panels with embedded heatpipes a viable option for flight hardware (thus accessing major benefits at technical and economical level). The core of the idea is to relief the stresses developed in the interface region between the CFRP skin and the aluminum heat pipe by inserting an intermediate layer that will permit to some degree a “differential” expansion between the two components preventing excessive stresses or failure. To maintain heat transfer to and from the heatpipe, enhanced thermal conductivity is required in the transverse direction. This is achieved by graphene-modified adhesives and nano-enabled CFRP layers.
A technology development project is proposed, to further develop this idea, based on materials (composites, adhesives) developed in previous ESA activities and a Proof-of-concept study performed in the frame of an EU project as a demonstration case. More specifically, using graphene and other nano-modified adhesives and composites an improvement of 30% in out-of-plane bending of bi-material samples has been shown.
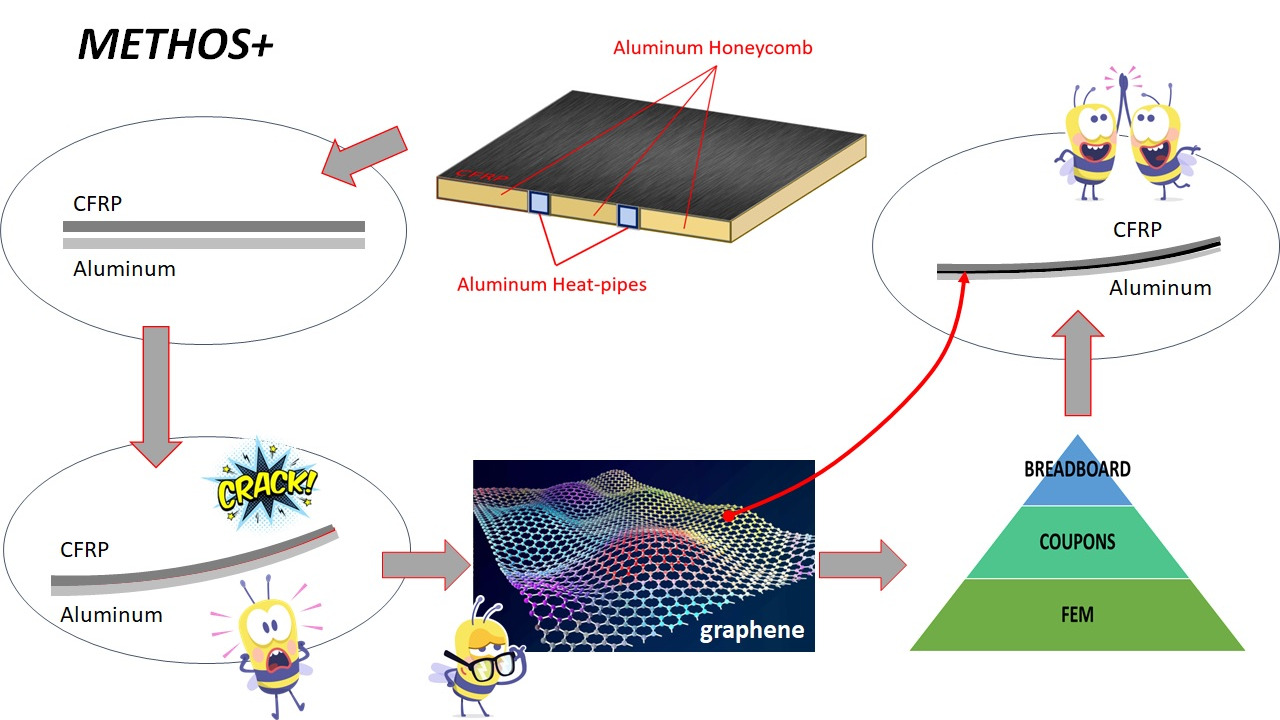