When considering sustainable human existence in habitats or space stations, additive manufacturing (AM) of metallic spare parts and hardware is a major enabling technology. At the moment the most developed metal AM technique is Selective Laser Melting (SLM), which currently cannot be adopted for in-orbit manufacturing due to lack of sufficient gravity to maintain a powder bed. To overcome this issue it is proposed to develop a novel form of powder feedstock and feeding system that can be operated in microgravity conditions. The proposed solution is based on mixing the metallic powder with a liquid binder and adhesive agents to obtain a colloidal mixture, in which liquid will act as a carrier for metallic particles. A similar approach is used in the medical industry for the application of colloidal silver or Aerosol Jet Printing technology used for 2D printing of electronics paths. With the use of nozzles, reusable gas, vacuum, and pressure difference, such mixture will be distributed over the substrate in form of mist or spray creating a liquid thin layer. The process would take place in controlled vacuum conditions, that will allow rapid evaporation of liquid, revealing an adhered by adhesion forces layer of dry powder. The feasibility of a similar binder-based AM approach was demonstrated in a vacuum in previous PECS activity. To this day, different additive manufacturing techniques have been also proposed by different teams for in-orbit manufacturing, such as direct energy deposition (Airbus) or powder-bed fusion using suction (BAM). However, the proposed AM technology with colloidal feedstock could offer better printouts resolution, material properties, and ease of operation than technologies proposed by others. The biggest technical benefit of the proposed solution is an increase of the long-term mission’s sustainability, by allowing on-demand manufacturing and repair of metal parts, be it spacecraft structures, tools, or spares required during crewed missions.
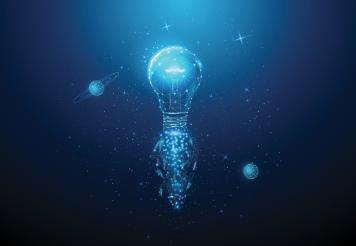