The design of efficient cooling devices is crucial in several space applications, such as cooling channel for the engine thrust chamber, heat exchangers for CCD cameras used for temperature-sensitive telescopes, and for electronic units in telecommunication systems (e.g. deployable radiators) during long-duration exploration missions. Although cooling technologies exist since decades, the use of strong power density and the miniaturization of components is today coupled to a lack of efficient heat dissipation methods leading to a truly technological bottleneck. This is even more critical for space applications where thermal management devices must be capable to dissipate heat in reduced gravity environments. Thanks to the new manufacturing technologies, the production of functionalized surfaces, which can enhance boiling heat transfer, has become a reality. However, their use is still poorly investigated, especially in low gravity environments. There, available empirical correlations are inaccurate since they come from terrestrial experiments where buoyancy has a strong impact. The aim of our project is to develop new textured surfaces with tilted conical micro-holes, which can retain and promote the development of vapor nuclei and enhance heat transfer during flow boiling in cooling channels. We will evaluate via 1g experiments their heat transfer performance and the produced pressure drops and compare the heat transfer performances to plain surfaces and surfaces produced by LPBF 3D printing. We will also measure surface wettability, visualize, and quantify the bubble production rate and coalescence. In a second phase, selected surfaces will be used in a flow boiling loop during parabolic flights to investigate the impact of gravity level on the heat transfer. The setup will be inspired by the FLORENCE breadboard integrated into the REXUS 27 sounding rocket. Support will be asked to ESA (CORA) and BELSPO (Prodex) for the microgravity activities.
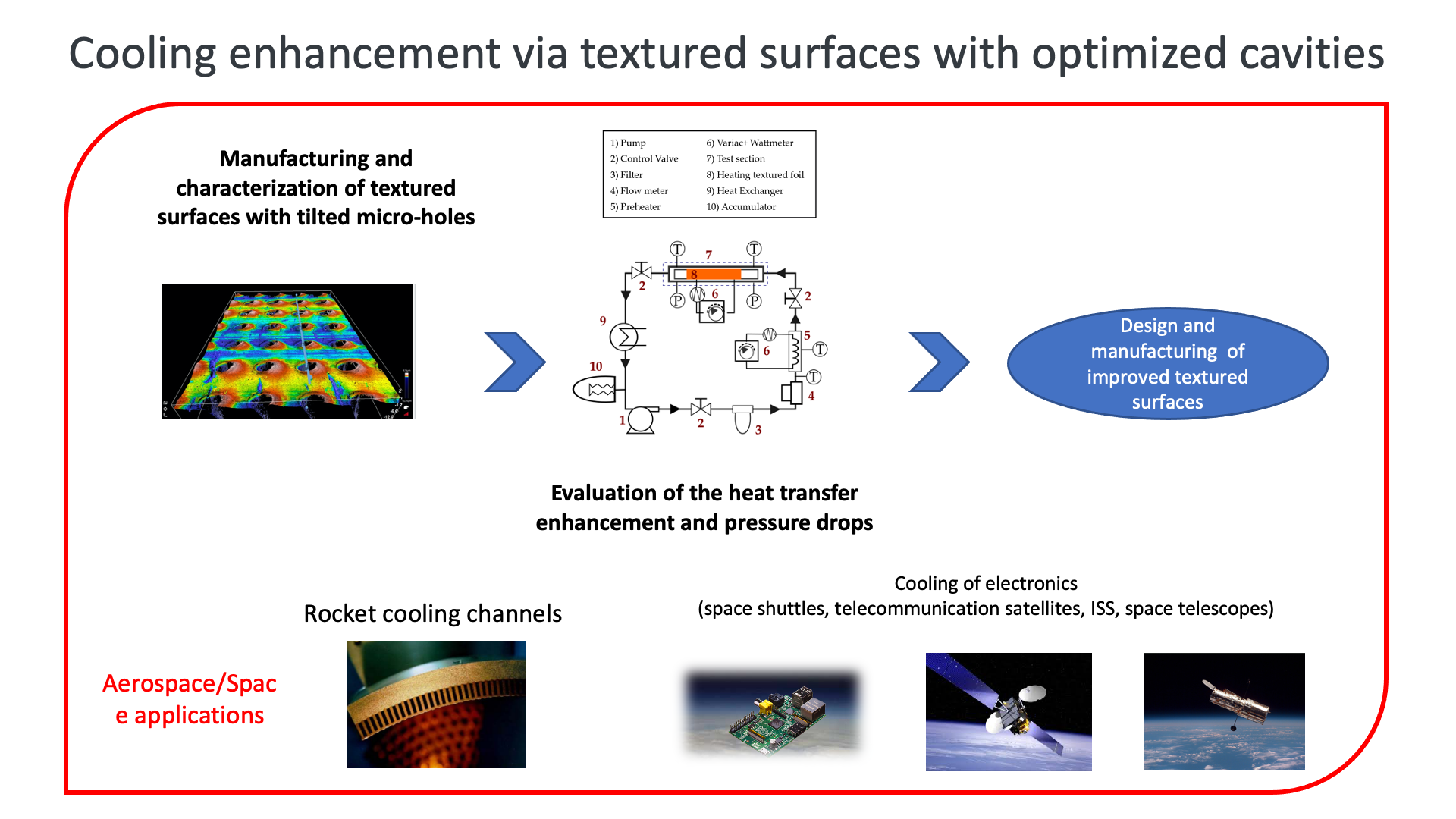