Current validation and verification (V&V) activities in aerospace industry mostly rely on time-consuming simulation-based tools. These classical Monte-Carlo approaches have been widely used for decades to assess performance of AOCS/GNC systems containing multiple uncertain parameters. They are able to quantify the probability of sufficiently frequent phenomena, but they may fail in detecting rare but critical combinations of parameters. As the complexity of modern space systems increases, this limitation plays an ever-increasing role. In recent years, model-based worst-case analysis methods have reached a good level of maturity. Without the need of simulations, these tools can fully explore the space of all possible combinations of uncertain parameters and provide guaranteed mathematical bounds on robust stability margins and worst-case performance levels. Problematic parameter configurations, identified using these methods, can be used to guide the final Monte-Carlo campaigns, thereby drastically shortening the standard V&V process. A limitation of classical model-based worst-case analysis methods is that they assume the uncertain parameters can take any value within a given range with equal probability. The probability of occurrence of a worst-case parameter combination is thus not measured. A system design can therefore be rejected based on a very rare and extremely unlikely scenario. The proposed idea aims to fill this gap by considering a richer set of probability distributions in the uncertain parameters and measuring the likelihood that a given problematic scenario will occur. It will also demonstrate on a realistic benchmark problem how to integrate the resulting tools in a typical aerospace V&V scenario and to significantly accelerate the system design. The objective is to provide the end user with a deep understanding of the way uncertainty at component level can propagate to a probabilistic outcome at system level.
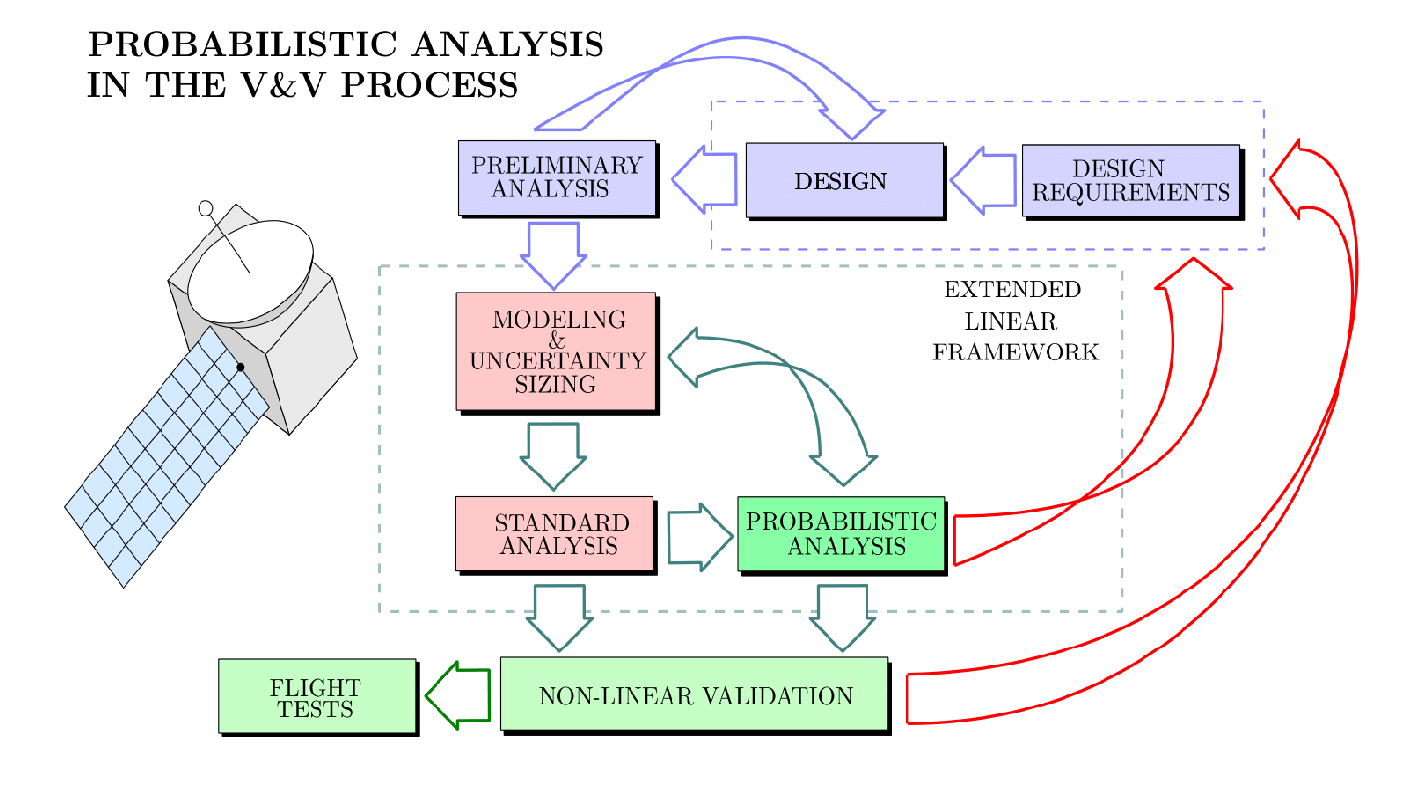