Improved surface quality and relative material density were achieved for lattice structures by optimising the process parameters and investigating the optimal scan strategy. A multicontour scan strategy with dedicated lattice parameters led to a relative material density of approximately 100%. This shows the need for dedicated process and scan strategy optimisation to achieve a good part quality for small-scale lattice structures. The geometrical deviation of the cross-sectional shape of the strut was mapped for a 35.25◦ inclination angle, different strut diameters, and different orientations on the baseplate with respect to the coater movement and gas flow direction. The cross-section of the strut was confirmed to be elliptical instead of circular. A linear compensation improved the geometrical accuracy on the strut level. The cross-section of manufactured struts based on a design which includes the compensation closely approached the intended circular cross-section. The linear compensation hence bridged the gap between the designed and manufactured struts.
A methodology was developed to test single strut samples with a gauge diameter of 0.5 mm. Comparison with standardised bulk samples with a gauge diameter of 4 mm confirms that the size effect reduces strength and maximal elongation. Further investigations can implement the same methodology for different strut diameters and inclination angles.
Additive Manufacturing (AM) has significantly increased the potential of metal lattice structures (MLS). For structural applications, the first steps are being made to investigate the use of AM MLS for weight reduction, and for improving mechanical characteristics, e.g. stiffness, strength or energy absorption. This research aims at elaborating the technology to take it to the next level: a fundamental understanding of the features determining the mechanical behaviour of real-life structural parts with integrated AM MLS enabling future applications. Firstly, the interface between MLS and bulk material will be studied by developing new graded porosity designs and different laser powder bed fusion manufacturing strategies. Secondly, the influence of the unit cell morphology and the part design will be investigated by the development and use of analytical and numerical tools covering material length scales from the lattice struts over, one or multiple, unit cells to solid structural components including MLS. Additionally, the impact of operational loads will be taken into account to investigate the possibilities for actual parts. Targeted applications can be increasing the strength- and stiffness-to-weight ratio of metal inserts and structural integration of radio frequency wave guides. The MLS design can furthermore increase energy absorption and steer the direction of failure within the lattice, protecting surrounding components. This creates potential to assist in shock absorption and damage control of a debris or landing impact. The study will start with AlSi10Mg MLS based on the vast experience of the KU Leuven research group with TiAl6V MLS and the experience with bulk AlSi10Mg of the main researcher (ESA YGT project of Emilie Beevers). In a next stage, MLS will be developed in high strength aluminium. Scalmalloy and A205 are candidate alloys available on the market. Pending the outcome of the ESA GSTP study ‘FOUR-A-M’, an alternative candidate will be considered.
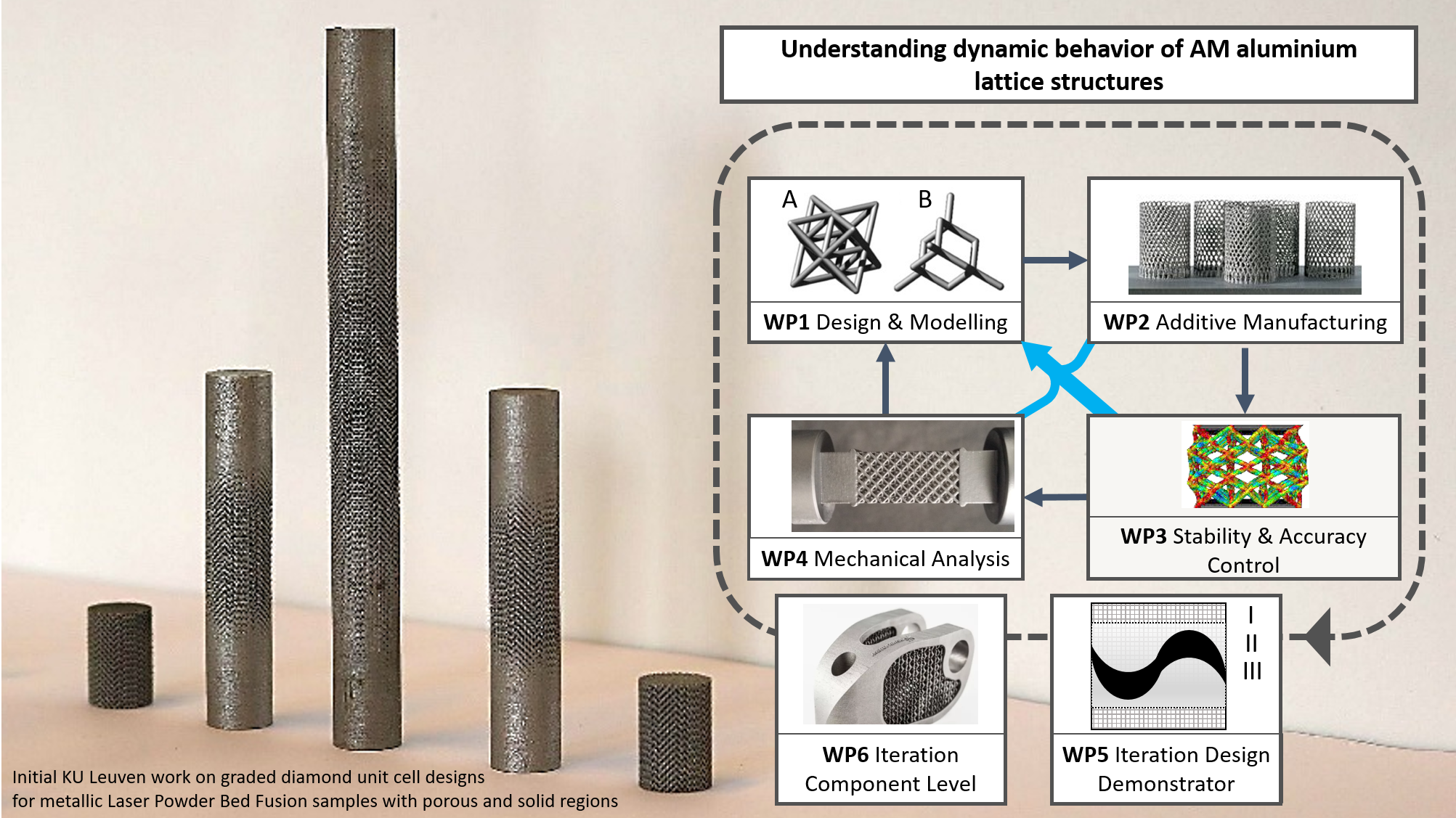