Space debris is mainly constituted by small items which cannot be de-orbited by using specific satellites launched from the Earth due to costs and difficulty in miniaturizing robotic arms or other rigid actuation systems. In a long-period vision, small cleaning satellites, with a size comparable with the debris to remove, can be manufactured in Space. Traditional robotic systems would be extremely expensive and some also would have problems in grabbing objects with undefined shape. Grabbing loads could result in debris fragmentation whereas fine tuning of the grabbing procedure would lead to not acceptable costs. Moreover, robotic systems are too much complex for in-space manufacturing. It is evident that an innovation is necessary in materials, and shape memory polymer composites (SMPC) are optimal candidates. SMPC can freeze a non-equilibrium shape (open) and recover the equilibrium shape (closed) by heating. Heaters and sensors are integrated in the SMPC structure during manufacturing. These smart structures can be easily produced in Space with a very simple structure which can be tailored on the size of debris to remove. The novelty is that SMPCs are very light and do not apply loads during grabbing with the result of optimal debris containment. Shape recovery rate is low, and debris approach and capture are gently managed . Rotating debris can be captured with low risk of structure damaging or debris disengaging by SMPC device re-opening. In fact, SMPC works as a damper during recovery and becomes stiff only after freezing.
This project aims to define for the first time the optimal SMPC geometry for debris capture. Our laboratory experiments so far have shown the ability of SMPC structures to grab simple objects but an optimal configuration for Space debris is necessary. Numerical modelling and virtual simulation of grabbing in Space environment will be made, as well as laboratory prototypes with integrated heating systems and controls to validate models.
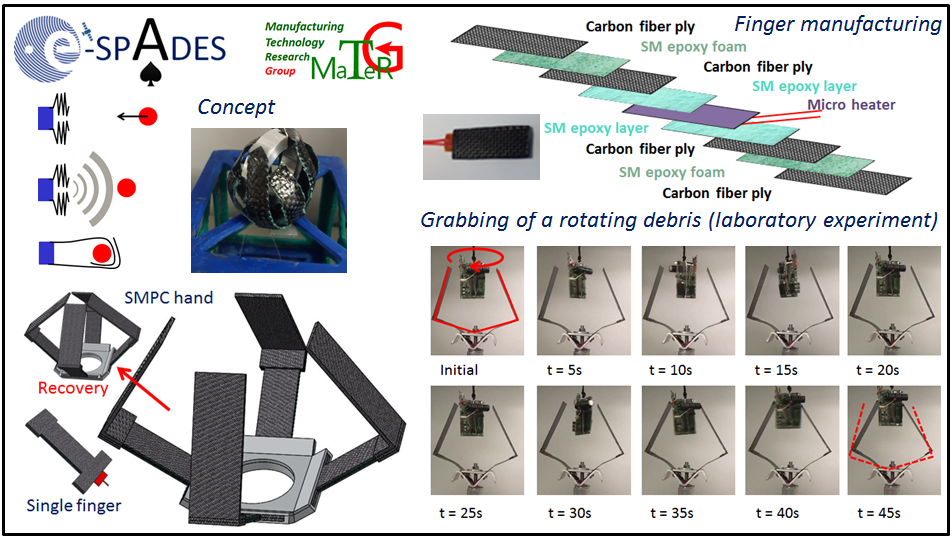