In 2018 ESA issued a GSP study “Conceiving a lunar base using 3D printing technologies” to evaluate the feasibility and implementation effort required in establishing the possible uses of Additive Manufacturing (AM) in easing the construction, expansion, operation and maintenance of a lunar base. Up to 52 AM technologies were assessed considering the following aspects:
- Flexibility to use the technology with different materials
- Logistic and transportation
- Lunar environment constraints on the process chain
- Resources available at the lunar surface can act as a AM feedstock as well, simplifying some process steps or raw material procurement (e.g. glass/ceramic printing)
Lithography-based ceramic manufacturing (LCM) technology was selected in the short list (composed by 4 AM process), because it bridges the material gap as it can produce precision ceramic parts as well as cutting edge biomedical devices and personalized medical products providing high-performance and biocompatible ceramics.
The process has been tested with Lunar Simulant (EAC-01) in the frame of the GSP project with Lithoz; showing the feasibility in processing the in-situ resources with parameters adjustment of the commercial machine. The process is based on different steps including pre and post processing equipment. The presence of a furnace, slurry and debinding, cleaning subsystems represent the main development which needed to be costed to allow having an integrated process in place on the Moon. Several adaptation and additional equipment needed to be brought from Earth such as furnace (debinding and sintering), slurry mixing system for the preparation of the binder and powder. A grinding and sieving equipment is mandatory considering the possibility to use Regolith or recycling feedstock. This study assesses each single process step and simplifies some passages in the manufacturing.
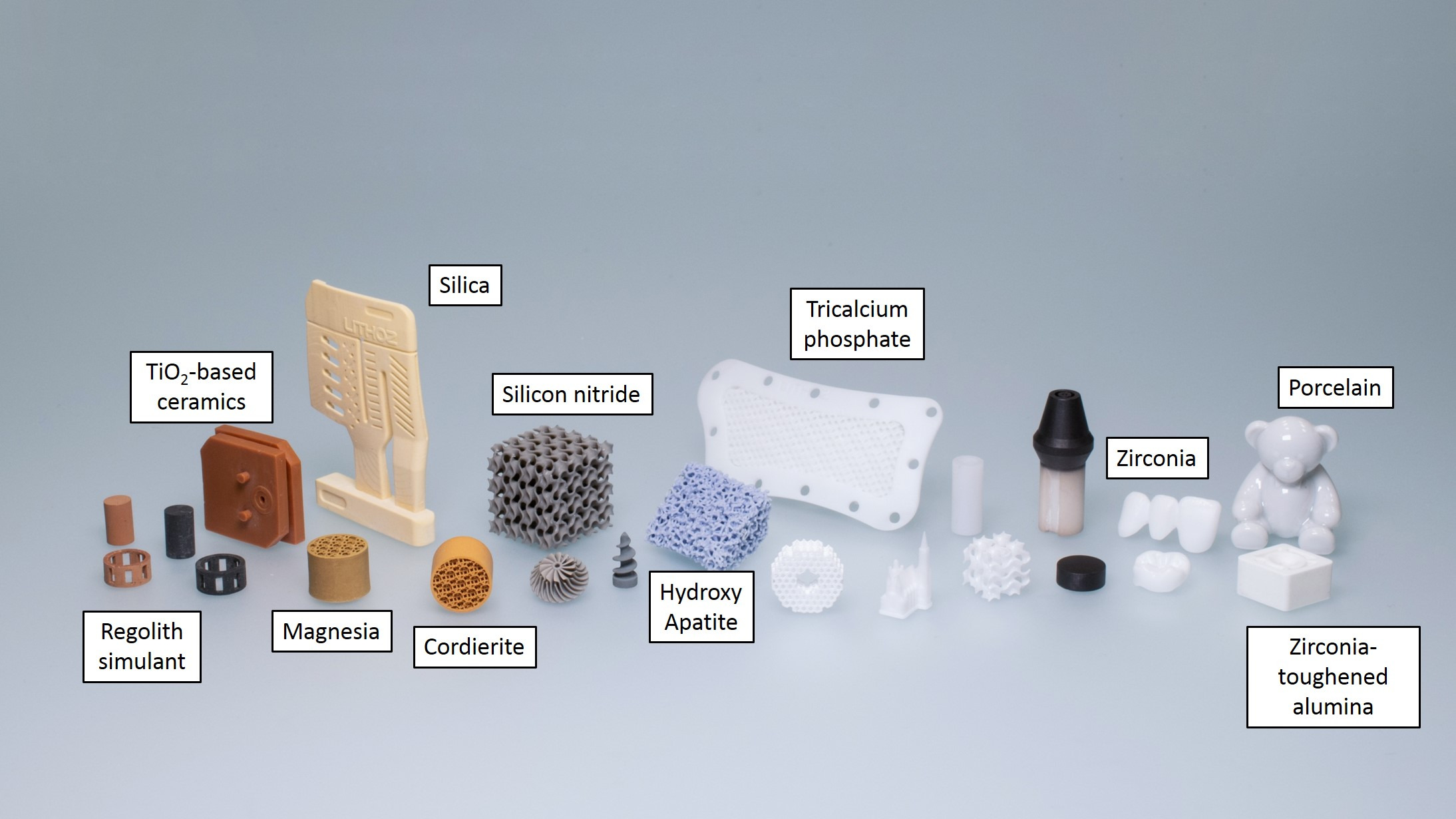