Extended missions to the lunar surface (and beyond) are an aspiration which will need to be supported through a combined scientific and technological progress in in-situ resource utilisation (ISRU) and additive manufacturing (AM). The entire lunar surface is covered by an unconsolidated layer of regolith rich in minerals and oxides which is produced by billions of years of meteorite and micro-meteorite impacts, leaving behind several meters of thick soil with average grain size of about 60 µm. Recently, several studies attempted on the laser processing of lunar regolith simulants which turned out to result in highly porous structures due to the complex chemical composition and presence of high quantities of oxygen in regolith as oxides in the form of minerals and amorphous glasses. South Pole-Aitken basin being a possible location for lunar manufacturing and construction site possesses an Fe-rich (up to 17% by mass) regolith (mostly pyroxene) surrounded by anorthositic highlands composed by plagioclase feldspar containing up to 18% aluminium. Amongst wide range of extraction strategies from minerals, the FFC Cambridge process has shown to be the most attractive for its very high oxygen yield (about 100%) and ability to reduce all lunar minerals and oxides which removes any constraints on regolith composition leaving behind reduced solid metallic products rich in alloys of aluminium and iron containing Si, Ca, Mg and Ti in appreciable quantities. Due to the extreme high heating and cooling rates in laser processing, the material might form an amorphous metal which could lead to exceptional mechanical properties. Accordingly, we propose a comprehensive investigation on the printability of this by-product followed by mechanical characterisation and the recycling effects of the powder feed-stock and the LPBF processed parts. The processed parts can be used in structural and load-bearing applications on the lunar surface and cis-lunar missions.
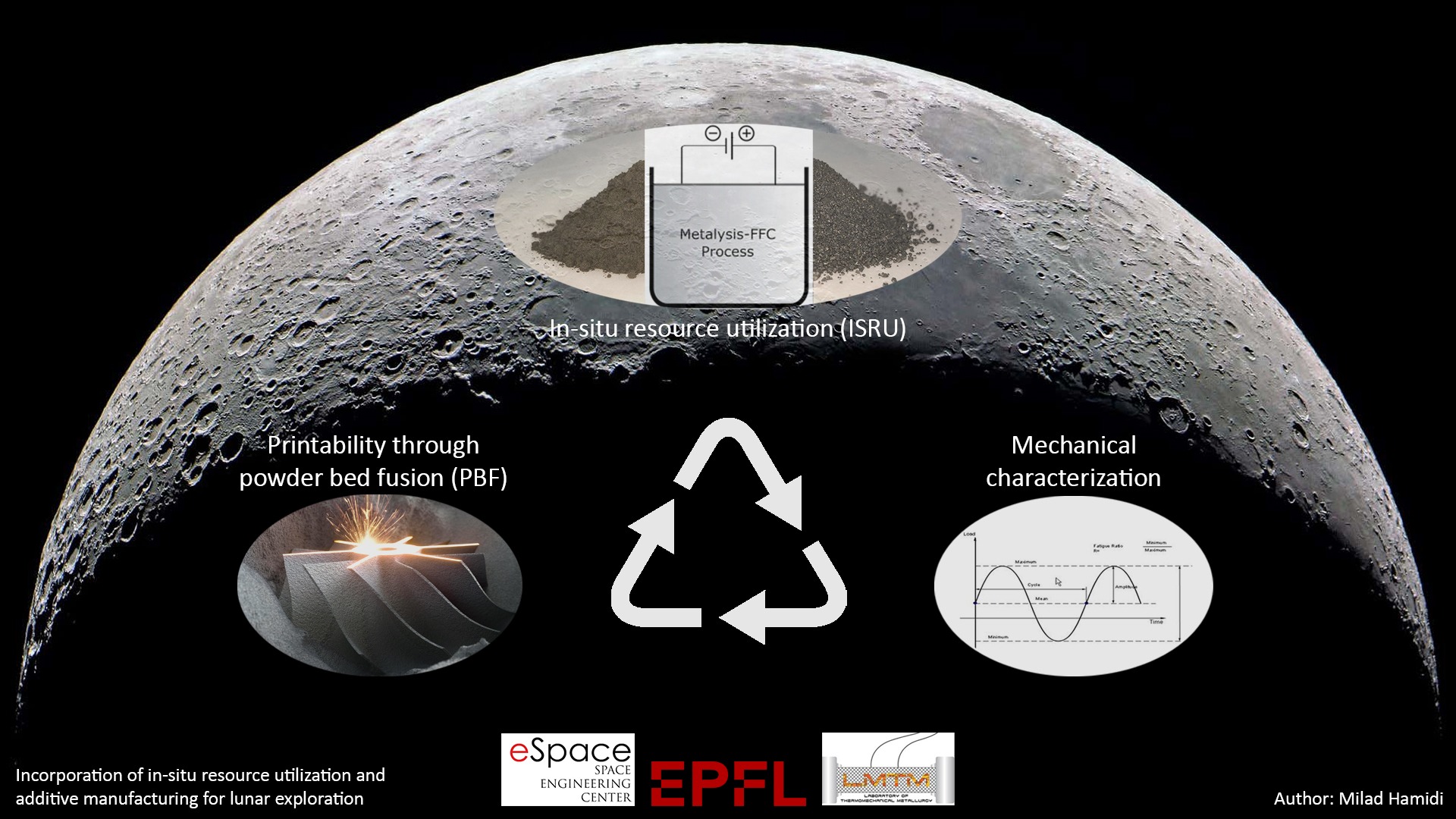