
Running
Duration: 18 months
Recent advancements in space exploration have led to a renewed interest in Large Space Structures (LSS). However, their implementation is currently hindered by specifications of standard launchers; construction complexity; and end-of-life phase which poses a potential threat due to space debris. Moreover, limitations in adaptability, scalability, and sustainability of LSS underscore the need for new approaches. To partially tackle these challenges, the concept of design for assembly and disassembly—successfully explored for on-Earth structures through modular components and repurposing strategies—offers a promising pathway. Building on this approach, LOFT will develop advanced design and engineering technologies within a comprehensive structural geometry and analysis framework for robotically assembled LSS. Leveraging the minimal dynamic loading conditions of in-orbit microgravity, we propose a loose-fit design system utilizing eccentrically connected components capable of reconfiguration into various geometries. Each component consists of a bar with one or more clamps that can translate along and rotate around the bar's axis. These clamps can be joined with those of other bars through an incorporated male-female hinge connector. This high-tolerance design reduces the need for precise placement by robotic devices, facilitating assembly via remote teleoperation.
LOFT will develop a multi-scale, multi-fidelity digital workflow to explore component geometry and assembly logics, facilitating the design of various LSS types. Additionally, the workflow will integrate design-for-reuse strategies to address logistics and decommissioning. LOFT will build upon ESA’s proven robotic arm technologies (e.g., ERA) and develop a custom-designed end effector specifically optimized for clamping operations. To validate this proposal, a proof-of-concept demonstrator will be manufactured, robotically assembled and disassembled within the consortium's laboratories.
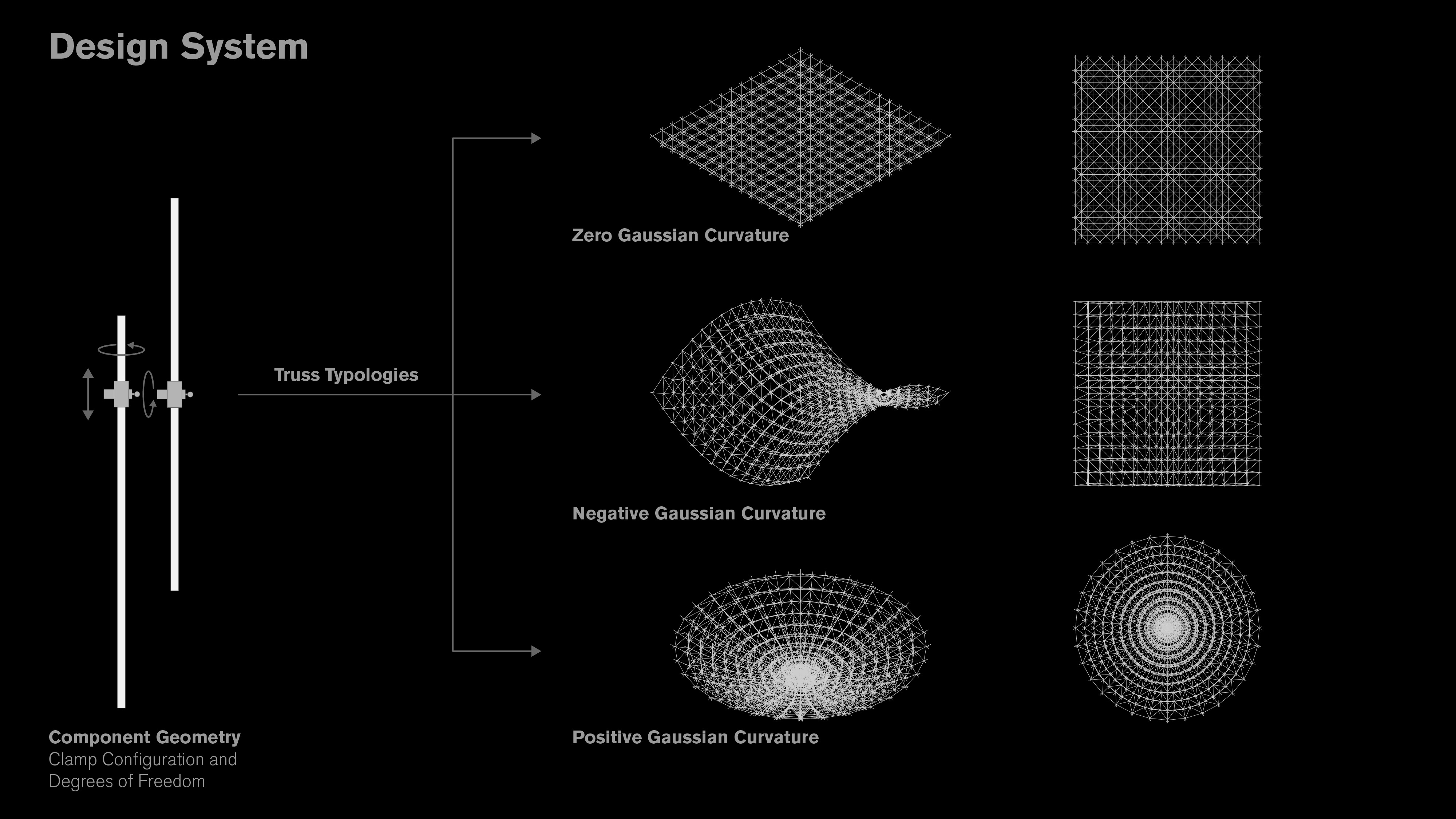