Space exploration entails a substantial investment, demanding extensive planning and resources to develop advanced robotic rover-based systems and identify suitable landing sites. Once these systems are deployed on a planet’s surface, they enable the assessment of environmental and physical parameters at specific sites. This project aims to demonstrate how recent advances in material science and printed electronics can be employed to fabricate a proof-of-concept thin-film sensor platform system delivered through a hybrid approach that combines printed and silicon elements including 2.5D integration through aerosol jet and inkjet printing. Central to the vision is the development of a thin, flexible, self-contained sensor system, directed by an in-depth analysis of current technology and literature; key objectives will be miniaturisation, mass reduction, low power consumption and low-cost versus current solutions. The overarching goal is to offer a self-contained technology suitable for large area deployment over extraterrestrial bodies as “sensor confetti”. Each sensor node will be fabricated on a thin-film flexible substrate and combine elements of traditional EEE components and printed electronics. The node will comprise of printed sensors and circuitry, an energy harvester, energy storage, a digital microcontroller, and accelerometer, forming a printed hybrid system. Utilising additive manufacturing processes such as screen and aerosol jet printing, combined with advanced integration techniques, the project will fabricate a prototype demonstrator as well as multiple samples for testing. Following production of a demonstrator system, a comprehensive evaluation of the sensing node will be performed to demonstrate its capabilities and identify limitations, from which a work programme will be developed to take the technology to the next stage.
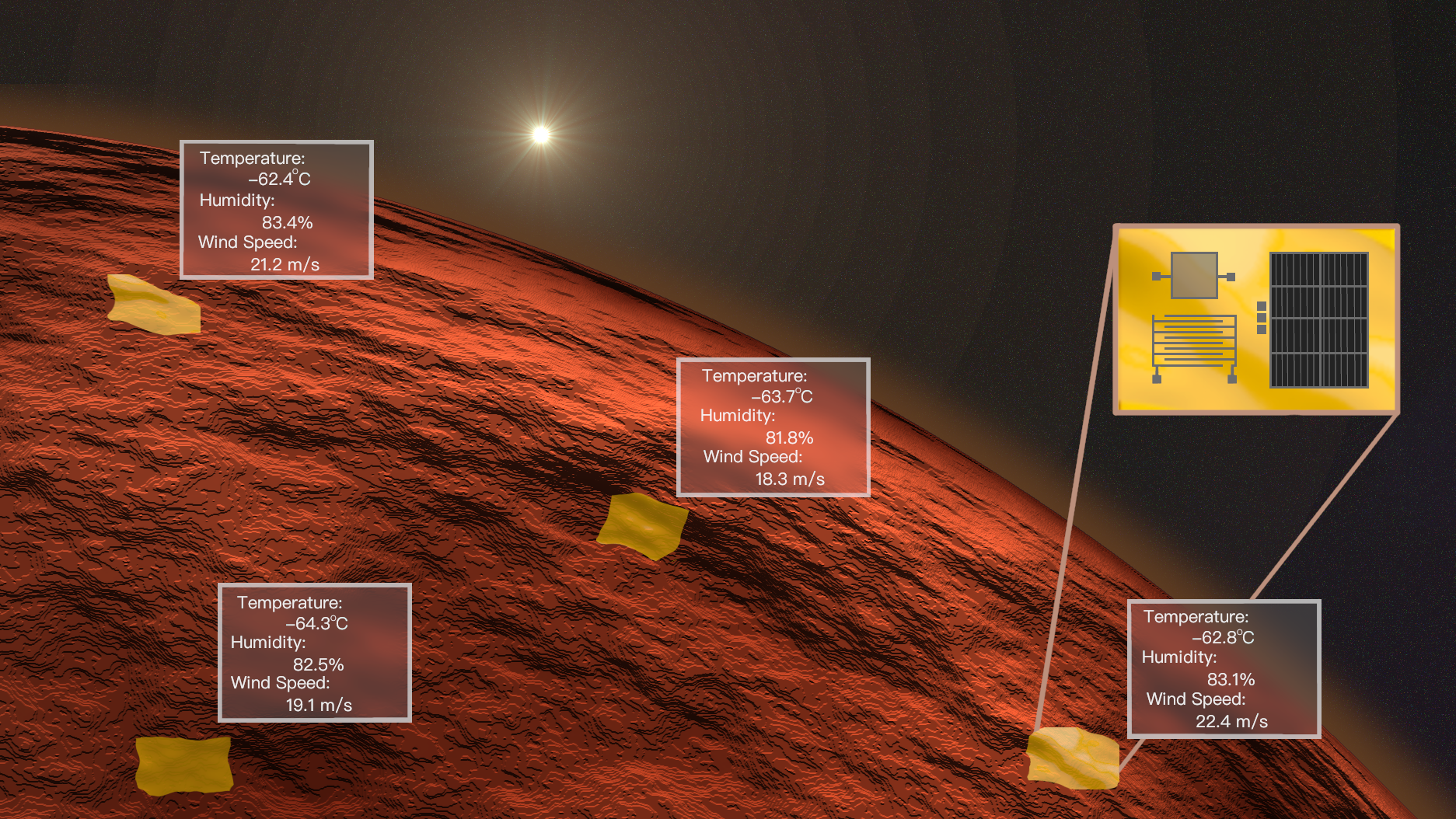