Laser Powder Bed Fusion (LPBF) is a cutting-edge method for fabricating complex metallic parts, in which a laser selectively melts thin layers of metallic powder. While LPBF offers unique advantages such as computer-controlled laser scan and printability of complex parts, there is a growing demand to extend this method to multi-material printing. To accomplish this extension, recent work tried to upgrade the hopper and recoater systems to deposit multiple powders, while multi-laser systems were also installed to scan multiple materials in a single layer. However, due to the large intermixing zones and LPBF induced thermal regimes, combining different powders often results in poor interfacial properties, associated to the formation of pores and cracks. Multi-laser systems also suffer from lack of coordination for achieving local control of thermal fields.
The proposed work consists of developing a hybrid LPBF method combining metallic foils with powders, focusing on the combinations of three alloys: 316L stainless steel, Ti-6Al-4V, and Al-12Si. The local thermal field during processing can be tuned by taking advantage of a laser beam shaping module developed in a previous project supported by ESA within the "Campaign: Off-Earth Manufacturing and Construction".
The hybrid LPBF strategy consists in depositing, cutting and welding thin metallic foils on a substrate made of LPBF consolidated powders, or other – already welded – foils. New processing windows are investigated, with the aid of thermodynamic simulations and microstructure characterizations. Compared to the mixing of powders, the hybrid LPBF method leads to different microstructures, due to new thermal paths induced by the hybrid process. Together with the beam shaping capability, the approach brings new degrees of freedom to produce flawless and pore-free high-resolution interfaces, with sharp or progressive changes in chemical composition.
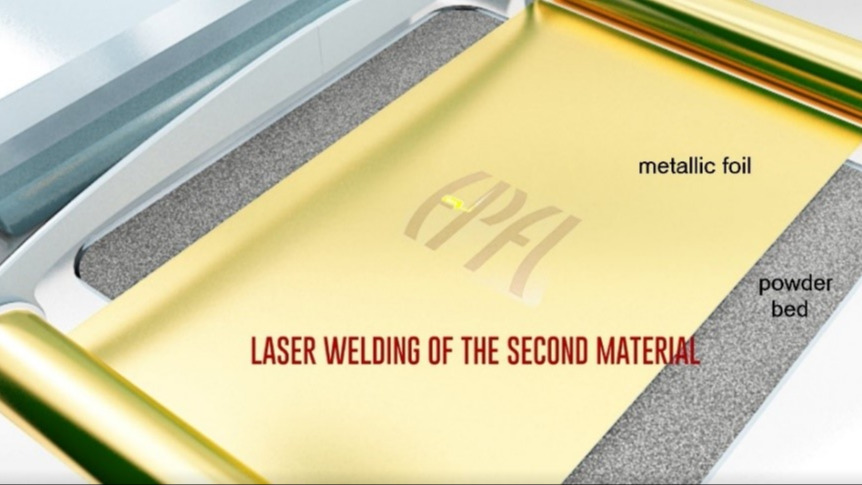