Literature review shows that optical fiber based sensors used in space applications mainly incorporate Fiber Bragg technology, which requires advanced laser interrogator. The solution proposed within this project assumes the use of High-Birefringence optical fiber as the strain sensor to monitor preload in the bolted joints connections, for example: HDRM during its whole life cycle (AIT/launch/operation). The use of dedicated H-B optical fiber, allows to greatly simplify sensing system to: light source + polarizers + H-B optical fiber + photodiode. Simple electronics elements allow to establish a cost-effective flight-standard electronic subsystems (consulted with SYDERAL). The optical fiber’s birefringence relates the difference in refractive indexes along „fast” and „slow” axes. The phase retardation of two eigenpolarizations in these axes, caused by strain variations is visible in optictal fiber as a change of the optical power. Test performed on simple laboratory model shows good linearity and provides evidence that the concept might be utilized in the proposed purpose (please check graphic). Proposed sensing method with different H-B optical fibers enables measurements beyond strain, temperature and pressure. Objectives: SoA-RR; DDV–PDR/MRR -Selection of H-B optical fiber: selection of appropriate length, sensitivity and coating for adhesion and load transfer. Propose solution to perform strain measurements independent from temperature. Task for UMCS which specializes in optical fiber technology. Definition of measurement system. XPANSE has experience from tests that incorporated optical fiber distribute measurement (OFDR); MAI–IPR: Integration, adhesives, coatings, pull out test, ingress/egress solution - Integration Process Review; Test Life Cycle-FR: Integration as per IPR, Functional tests in ambient gradual application of preload and control with calibrated load washer, Test in climatic chamber in -40/+ 80 degC, Drift and creep effect characterization.
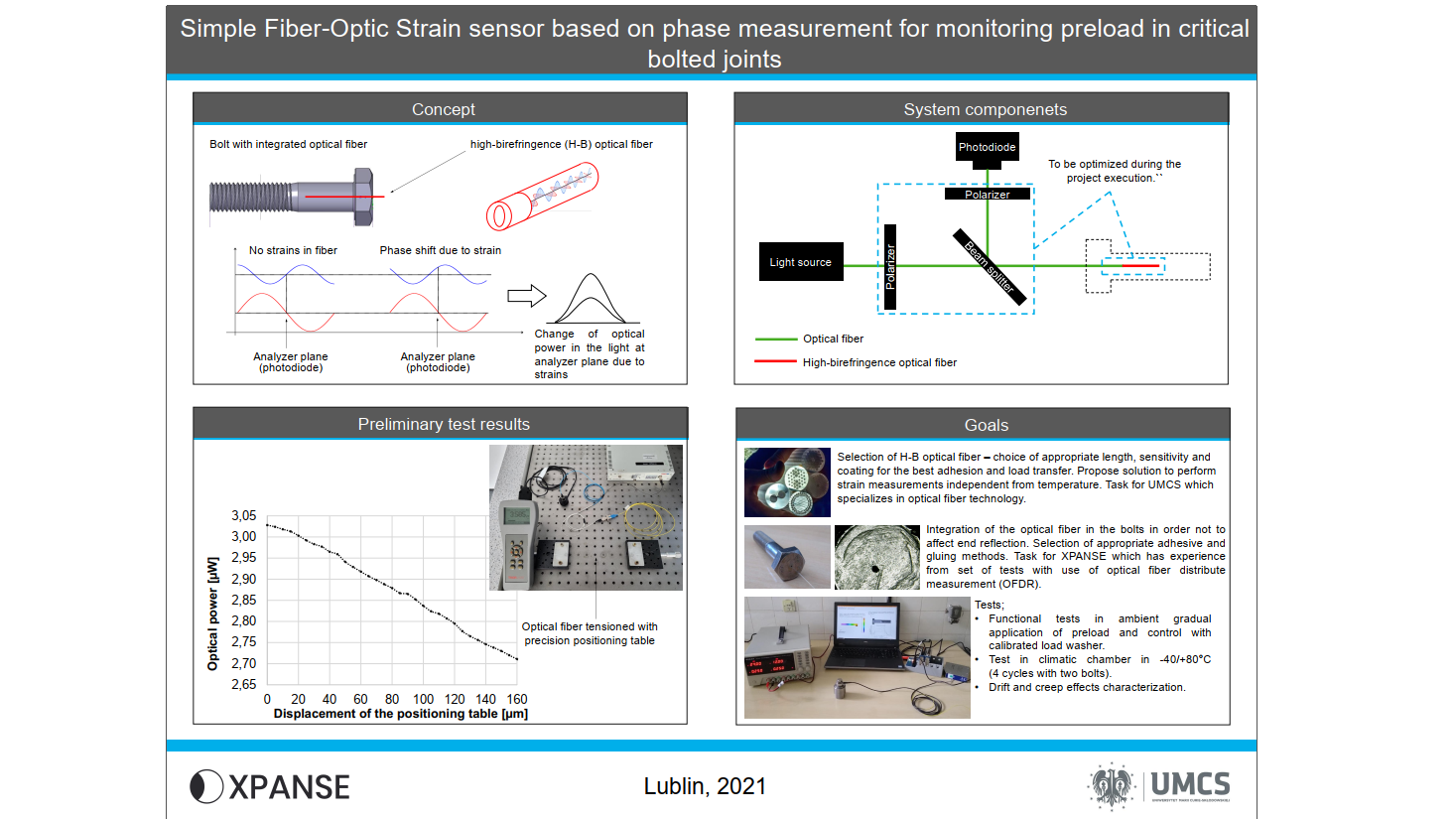