There are several space applications to our Optical Pressure and Temperature Sensor [1], but the most interesting one would perhaps be satellite propellant gauging. The need to know the remaining fuel on commercial and scientific satellites is vital, as it will allow the retirement of a satellite at the latest moment in time, thus extending its operational life. Also, every extra month of operation in space represents millions of dollars in revenue for a large telecom satellite. The state-of-the-art in Europe is the Moog Bradford pressure sensors, which have been developed under an ESA ARTES activity back in 2009 [2–5]. These sensors have a gauging accuracy of 7(42) months for a 10(15) year mission and their pressure accuracy is 13 mbar [2,5]. To improve the gauging accuracy considerably, the pressure sensor needs to be accurate to within 0.16 mbar (16 Pa). We have demonstrated in the laboratory an accuracy of 1 Pa measured at 1 bar for our Optical Pressure and Temperature Sensor based on the distributed Bragg reflector (DBR) fiber optics technology [26–37]. Space applications have never been investigated as far as we know for this technology, which is still being developed in laboratories. Space qualification of the Optical Pressure and Temperature Sensor based on DBR technology is conceivable since optical sensors based on a much older and less accurate Fiber Bragg Grating technology have been successfully used to measure pressure in propellant tanks on PROBA 2 back in 2009. Our DBR technological platform based on ultrafast optoelectronics could be the key to unlocking several space applications for optical fiber sensors (OFS) [1] by finally reaching technical goals promised by OFS such as improved accuracy, immunity to electromagnetic interferences, robustness, reduced weight and reduced costs.
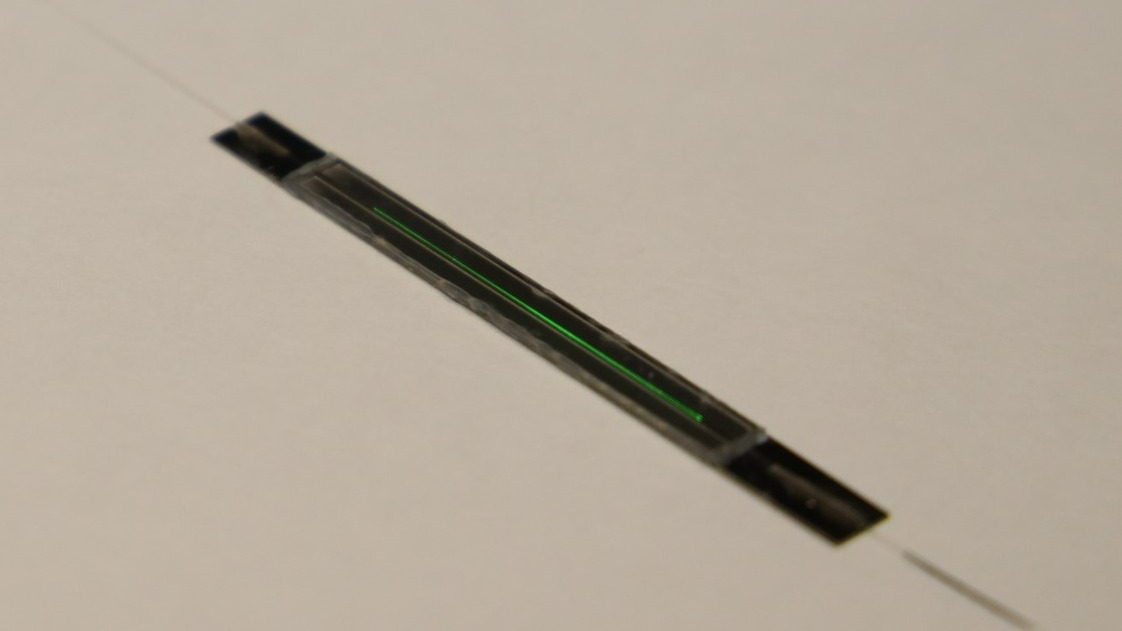