The design of reusable/expandable launchers, any type of (re-)entry vehicles and propulsion units is currently strongly governed by aerothermodynamic considerations. Tremendous performance gains can be achieved for each of these vehicles with game-changing boundary layer laminarization techniques. The associated benefits are numerous (lighter thermal protection system, trimmed vehicle drag, abated acoustic loads on the structure, and reduced fuel consumption) and will directly benefit to more economical access to space at the advantage of enhanced payloads. Our ambitious objective is to maintain laminar boundary layers all along the body by designing efficiently the mold line to preserve or, where needed, to initiate a fresh laminar boundary layer. The biggest challenge is to achieve this goal by delaying the triggering and growth of instabilities and/or preventing local flow separation. To this end, we endeavor to resolve numerically the flow motion around a generic shape and to rely on an unprecedented optimization strategy to identify an advanced geometry that meets its goals for a wide range of operating conditions. The automated optimization-based approach will vary both the geometry and the operating conditions to which it is exposed while minimizing an objective function characterizing the wall skin friction and streamwise pressure gradient. This methodology is foreseen to be applicable to any type of internal/external configurations traveling at different flow regimes and we suggest demonstrating it on one configuration of interest starting with an internal transonic configuration. The benefits of the optimization-based design approach will finally be demonstrated experimentally. Non-intrusive measurements of the flow velocity field will be performed and will serve to evaluate the performances of the optimized geometry when subjected to different high-Reynolds numbers operating conditions.
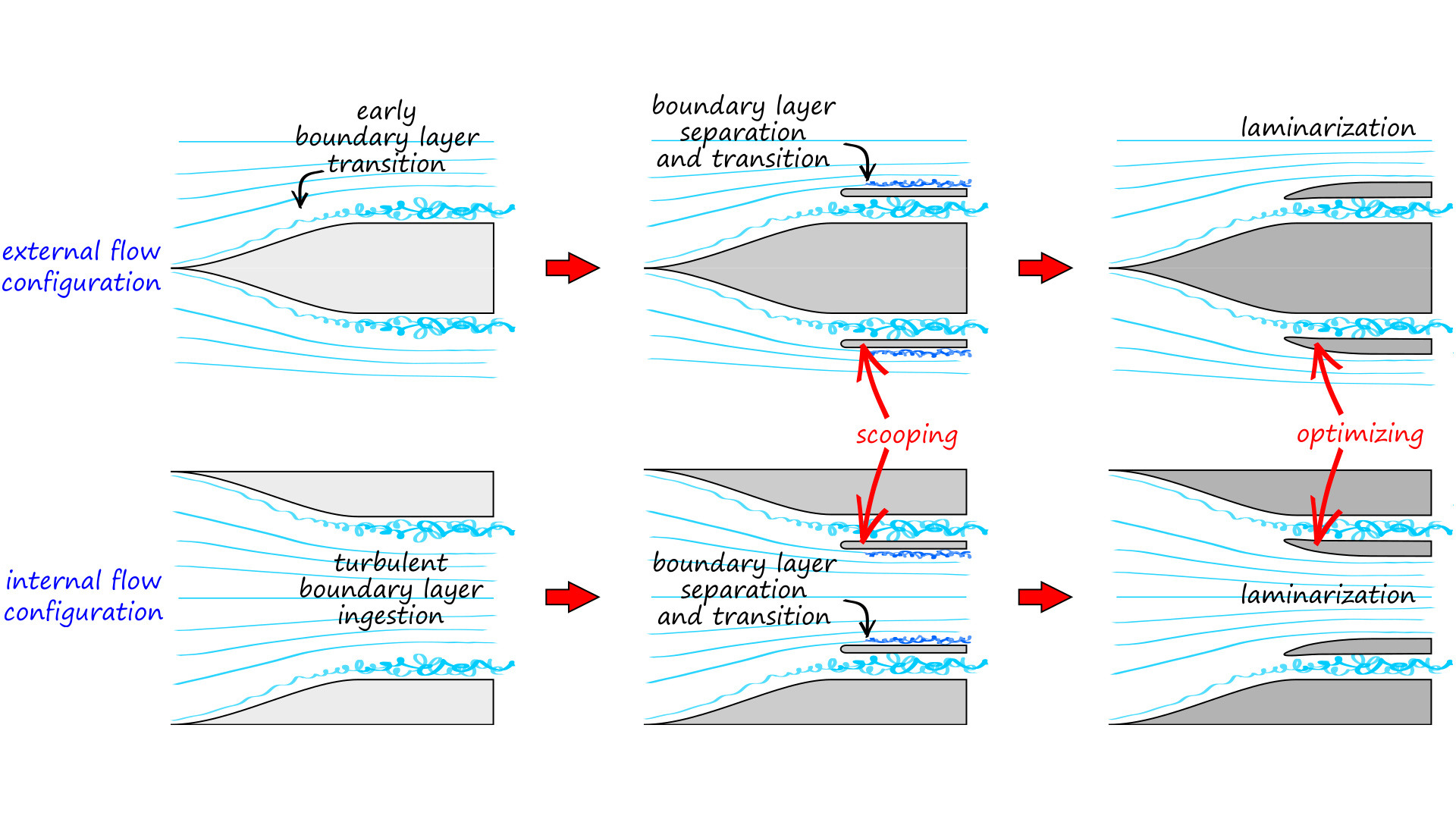