Automotive has its own standards for qualification of Hi-Rel COTS components (AEC-Q) as well as for the certification of high-criticality hardware and software designs (ISO 26262, parts 5 and 6 respectively). Their methodologies are similar to ECSS e.g. ECSS-Q-ST-60-13C for COTS EEE components, ECSS-Q-ST-40C for software and ECSS-Q-ST-20C and ECSS-Q-ST-60-02C for hardware development. However, to our knowledge there is no established equivalence between automotive and space standards for COTS processors. If existed, the space sector could take advantage of the high reliability of automotive COTS hardware and software, high volume and low cost to reduce their qualification and certification cost. Moreover, this would reduce the time and effort of space qualification and accelerate the adoption of new, high-performance technologies from the automotive sector to increase autonomy, like Graphics Processing Units (GPUs) or machine learning accelerators. We propose to create a mapping starting from basic elements of the standards, e.g. criticality (ASIL vs CN), FMECA, risk, hazard and Fault-tree analysis etc. Next, the analysis will be extended to specific parts, such as ECSS-Q-ST-60-13C regarding the qualification of processing elements. In addition, COTS may refer to a hardware or software element designed from the vendor to comply with a certain ASIL, e.g. ASIL-D, the highest integrity level in ISO26262. Assessing how this design complies with the requirements of the space hardware or software elements of a given CN and if any changes are needed for its certification, is also crucial for maximising reuse from the automotive domain. For example, Brook Auto/BRASIL is a GPU language designed for ASIL-D certification and its compiler for ASIL-D qualification, too. It could be used as is in a science/observation mission, but not in a launcher or human spaceflight, since automotive standards are designed as fail-safe instead of fail-operational, as opposed to avionics.
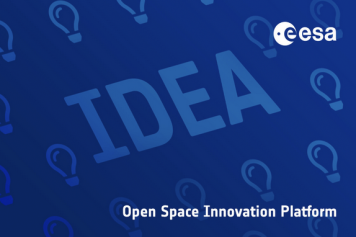