Recent advancements in the MEMS technology have allowed for the development of secondary micro-propulsion systems for small satellites. Among them, vaporizing liquid microthrusters (VLMs), are an interesting choice thanks to their simplicity and the advantage in using lighter and smaller propellant tanks. VLMs provide thrust force ranging between 0.1 and 10 mN and have an estimated specific impulse (Isp) above 100 s for water.
However, to reach such values, the fluid green propellant is heated at temperature much higher than its boiling temperature, inducing explosive boiling into the flow channels. This reduces the VLM lifetime and dramatically worsens its nominal performance leading to low thermal efficiency and thrust unsteadines.
Our idea is to overcome these problems and strongly increase the VLM efficiency as follows:
- we decouple liquid vaporization from gas superheating using two heating sytems, enabling for Isp maximization with device temperature reduction. A main heater is applied to the whole thruster and drives the dry-out incipience into the device. Another composes of in-channel heaters in direct contact with the vapor to strongly increase its temperature.
- we apply a fast pulsed actively controlled heating to maximize the thermal efficiency and stabilize the boiling flow. This control bases on in-channel heaters and sensors (temperature, pressure, void fraction), real-time management electronics, and control algorithms built on machine learning techniques.
We have developed and tested a MEMS-based VLM prototype equipped with micro-heaters, temperature and void fraction sensors. Preliminary studies have already shown power saving up to 40% and increase of VLM efficiency up to 60%, which validate our methodology.
Further performance enhancement is achieved via the optimization study of channel geometries. Apart from water to be used for the basic understanding, various other green propellants will be assessed to see the impact on the Isp improvement.
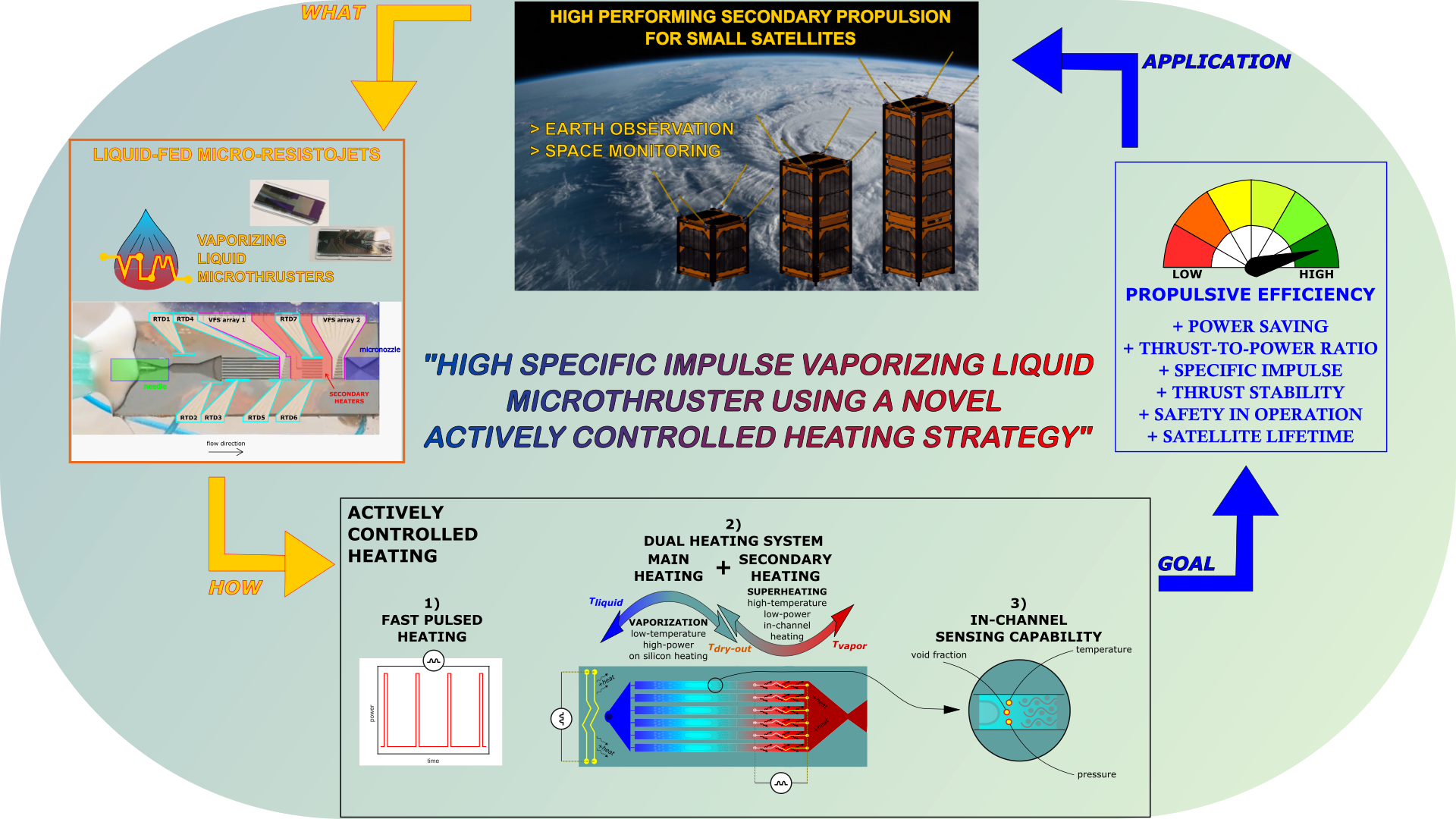