Due to the ongoing miniaturization and increased performance of electronics devices alternative cooling methods are required, specifically mechanical pumping loops (MPL). Passive two-phase loop is not capable of cooling the ESA expected power densities up to 300 W/m2, pumped two-phase loops are forecasted to replace their passive counterparts. According to Lapensée et. al., “the most important component of a MPL is the pump and a pump failure directly results in MPL system failure, a reliable pump is therefore of vital importance". Wits et. al. noted that in addition to a reliability of >20 years, the micro-pump is required to withstand a working pressure of 60 bar, and to achieve a minimum flow rate of 5 ml/min. Stokes Micro Fluidics (SMF) has developed a ultra-reliable magnetic shuttle pump (MSP) features a two counter-wound solenoid coils, which are used to oscillate a neodymium shuttle magnet. The MSP has a smaller footprint than any commercial pump at 0.8 cm3. Its design can accommodate a working pressure > 60 bar and can achieve a minimum time-to-failure five times greater than that of conventional piezoelectric microfluidic pumps. Currently pumping for MPLs in space applications are developed by National Aerospace Laboratory (NLR), their system is a modular design that allows for individual pump failure. The maximum output of their (100g) five pumps system is 15 ml/min and 5 kPa, however a single 5.6 g SMF micropump can output 49 ml/min and 45 kPa. A modular five parallel SMF micropump system is capable of pumping 245 ml/min and 45 kPa at < 50g. The stokes microfluidic system would allow significant weight savings due to the leading performance and reliability that could be achieved using even only one unit.
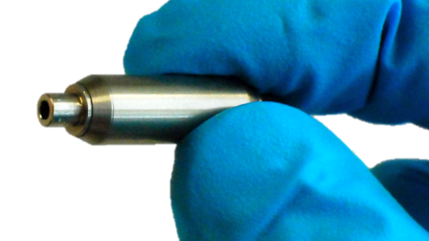