Long-term human presence in space will require on-orbit and on-planet manufacturing, but to have the maximum advantage of these technologies the capability to be self-sustainable become fundamental. The Fused Filament Fabrication (FFF) is the safest, widespread and mature additive manufacturing technology on Earth as well as in space. In fact, the FFF has already been tested under low gravity conditions onboard the International Space Station (ISS), mainly with consumer-grade plastics. The technology covers a wide range of materials and allows printing parts identified for the laboratory usage, tools, structural elements as well as being the technology based on food and tissue printing. Understanding how the Fused Filament Fabrication process works in a vacuum with high-performance polymers, and whether it’s suitable for processing the filaments provided by a recycled system, is one of the critical steps in additive manufacturing technology implementation for future space missions. The idea presents a further technological step to demonstrate 3D printing of high performances thermoplastic polymers in a vacuum combined with the current state-of-the-art of recycling system. The main steps are reported below: · Utilization of the current design of the developed high performances FFF printer (MELT and IMPERIAL projects) · Adapt the configuration and elements for vacuum suitability (up to 10-6 mbar) and adapt the distribution and process to the tolerances and quality of recycled filaments · Manufacturing, Assembly and Test the printer under vacuum conditions (up to 10-6 mbar) · Compare mechanical and functional properties of samples printed in a vacuum and under ambient pressure with new and recycled filaments. · Identify the mechanical quality of the samples printed with recycled filaments and define the number of recycling cycle versus the type of hardware to be produced.
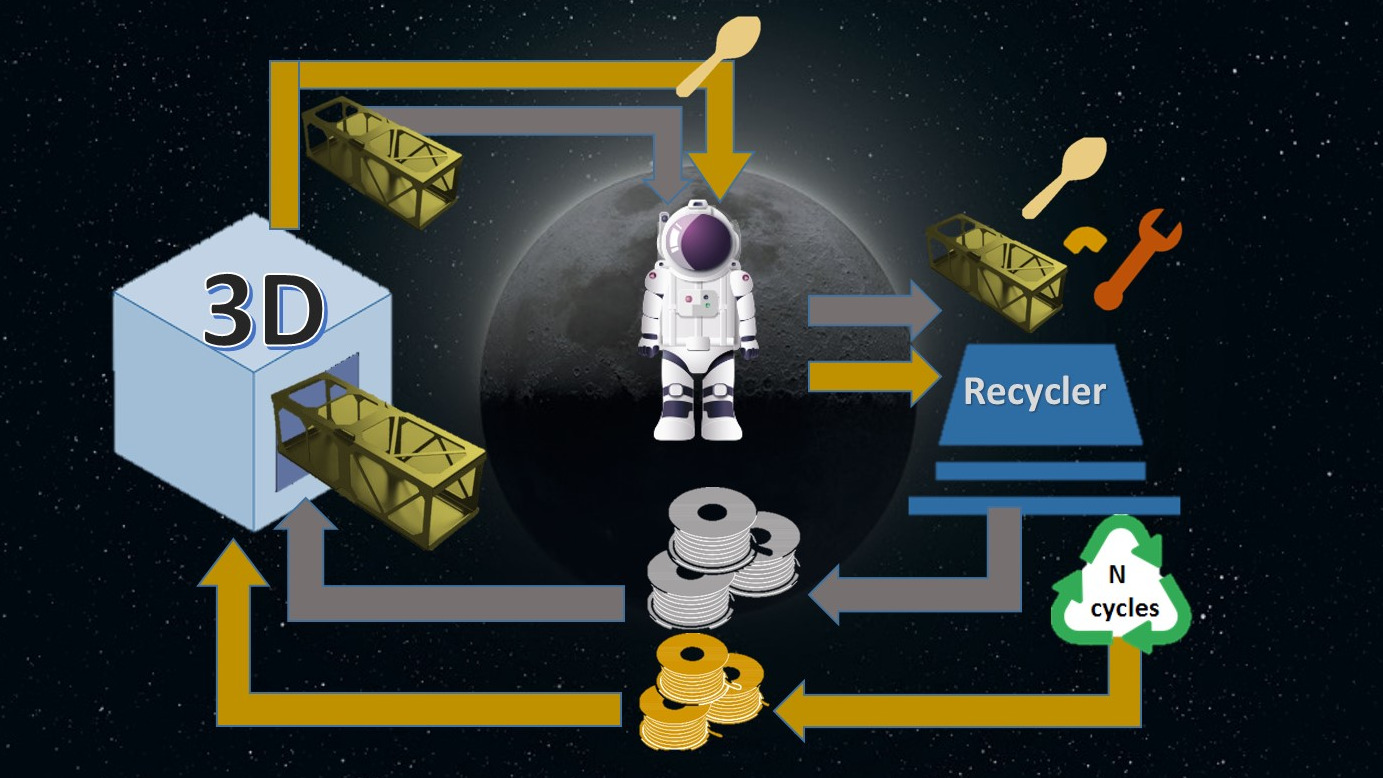