Silicon carbide (SiC) ceramics show excellent mechanical and thermal properties, combined with low density, low sensitivity to environmental effects and ability to work over a broad temperature range. This makes them suitable for precision instrumentation, i.e. telescope mirrors and their substrates, hot structures of future launch vehicles and structural components. SiC can be fabricated by a fast net-shaping process using liquid silicon infiltration as a densification technique to yield reaction bonded SiC (RBSiC). Porous preforms for this process can be made using die compaction for simple shapes or injection moulding (PIM) for more complex components. However, PIM requires an expensive mould, so only large series production is economical, which is not typically associated with space applications. Additive manufacturing (AM) is a production process offering the benefits of PIM (complex geometries) without the need for a mould. Additionally, components are produced at low lead time, allowing fast design iterations. This makes AM technologies ideal for prototyping or small series production of highly complex parts for the aerospace industry. Laser sintering (LS) is an AM process in which a laser selectively scans a powder bed, layer by layer, to form a 3D part. A methodology for LS of RBSiC was recently developed at KU Leuven (Fig. 1). LS is used to shape a porous preform which is subsequently infiltrated with carbon and liquid silicon. The end result is a fully dense RBSiC component consisting of residual Si, α-SiC and β-SiC. The fabricated components contain up to 85 vol% SiC and 15 vol% Si, flexural strength is up to 220 MPa, with a Young’s modulus of 285 GPa, hardness of 2045 HV and low specific weight (2.9 g/cm³). They are net-shape, as no densification shrinkage occurs during liquid silicon infiltration. Using LS as a shaping method, complex components can be fabricated at low lead time and low initial investment cost on commercially available equipment.
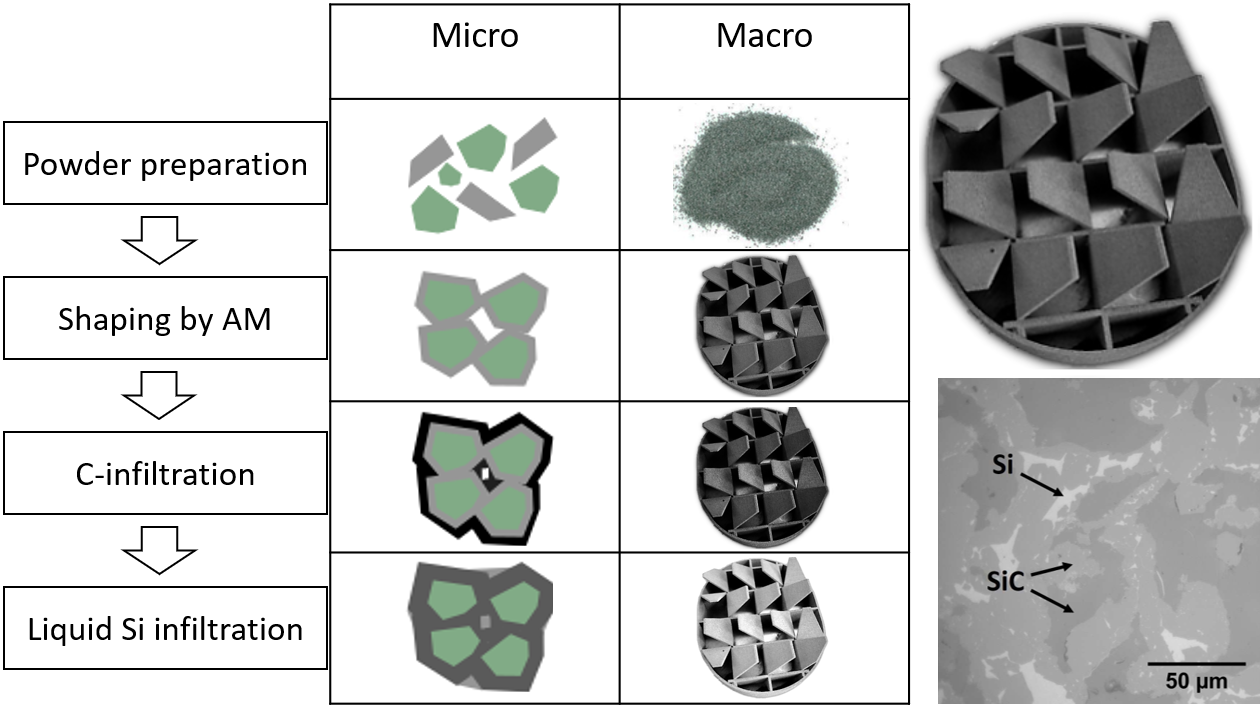