Additive manufacturing, particularly fused deposition modelling (FDM), makes it possible to produce unique parts quickly and at low cost by sequentially depositing beads of a molten polymer. However, commonly used polymers show low mechanical properties and are thus more suited for rapid prototyping than stress critical component manufacturing. Biological materials such as bone, spider silk and wood are lightweight composites arranged in a hierarchical structure that is formed by directed self-assembly. Inspired by this exquisite macro-molecular control, an effective approach to orient polymer molecules at low strain rate is to utilize macro-molecules that can self-assemble into ordered crystalline domains upon changes in temperature, such as thermotropic liquid crystal polymers (LCPs). During extrusion of the LCPs from an FDM nozzle, the liquid crystal domains assemble in the direction of print, resulting in extremely high anisotropy and high mechanical properties; a factor ten higher in strength and stiffness to high performance polymers, rivaling also continuous fiber composites. The resulting immense shaping freedom allows loading perpendicular to the print paths to be minimized and the overall part performance optimized. Both fabrication and design aspects of this breakthrough now need careful attention by deeper study for space applications.
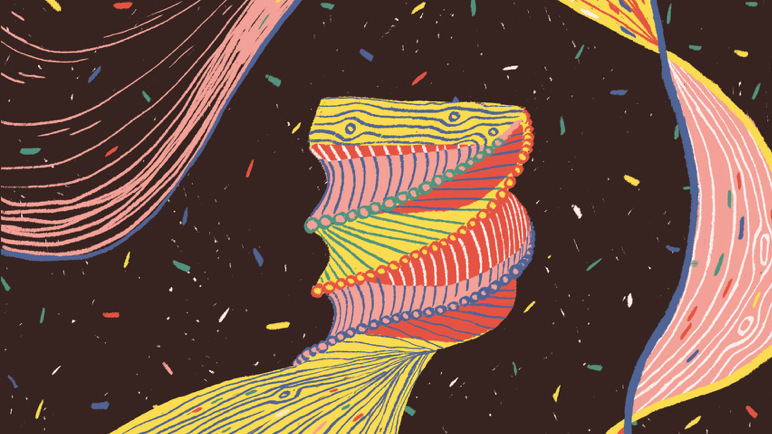