The project aims at developing a miniaturized fully electronic system for real-time monitoring of the amount of dust particles depositing on it. The project targets avionics and space missions requirements of having complete control of the cleanliness and deposited particles level during fabrication of the flight hardware, during assembling of the payload, and in the launch phase, as well as over use in long missions. Miniaturization allows for multiple-sites dust monitoring, both at the subsystem level in the payload and at the instrumental level in each scientific instrumentation like mirrors or transparent shields. The prototype will leverage an integrated CMOS chip that the group designed and successfully tested a few years ago, that counts in real-time dust particles down to 1 micron diameter. The chip operates by tracking with time the capacitance between two electrodes that will be affected by the arrival of a dust particle. The chip has proved to reach a resolution of 65 zeptoFarad of detectable variation within a millisecond time-scale, ensuring single particle monitoring and a dynamic range of about ten million dust particles over a sensitive area of 1.15 mm^2 [1,2,3]. The project will develop a prototype of a miniaturized particle monitoring system targeting avionics and space missions needs based on this integrated chip as a core device. It will feature a microcontroller for the chip operation, an ADC for the conversion of the chip readings, a transmitter for data read-out and monitoring and all other hardware and software functionalities that ensure a completely autonomous operation of the system through a custom interface on a portable device. Miniaturization of the full prototype, precision in the counts, simplicity of operation, low power consumption, multiple-chips read-out and long-term dust tracking over months are the aspects that will be considered in the development of the system, to target at the best the needs of the mentioned space application.
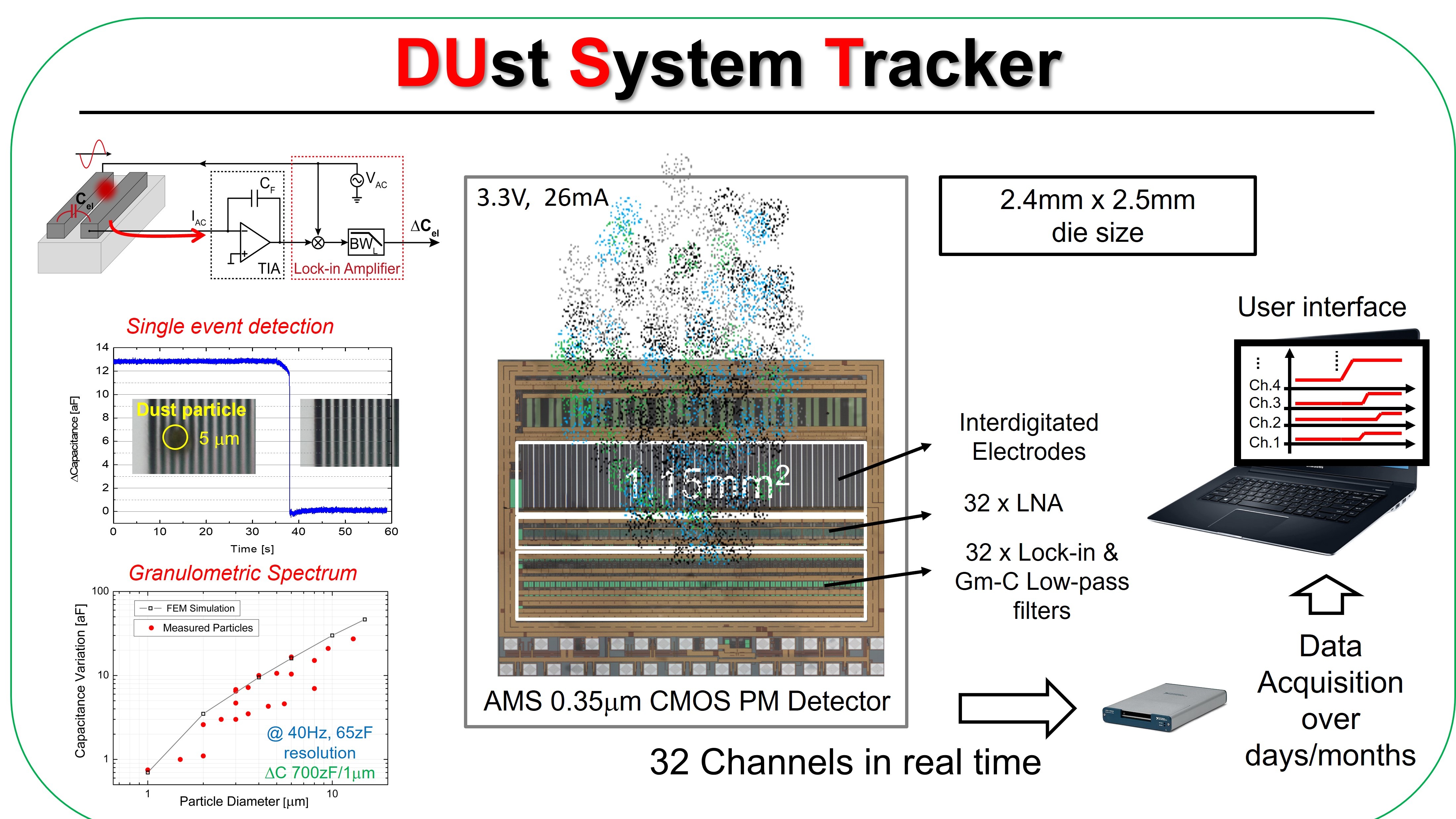