Duration: 18 months
Shock absorbers play a critical role in aerospace systems, safeguarding structural integrity during launch, flight, and landing by mitigating extreme forces on key components such as launcher brackets and sensitive payloads. This project aims to develop a smart damping system by combining the geometric flexibility of additive manufacturing (AM) with the adaptive performance of NiTi shape memory alloys (SMAs). The unique properties of NiTi SMAs enable the design of damping components that recover their original shape after deformation based on operating temperature, ensuring reusability over multiple loading cycles. Additionally, AM allows for the direct integration of energy-dissipative features, enabling customizable designs with tailored mechanical properties to accommodate specific payload sizes and varying mechanical and thermal conditions. After evaluating various lattice designs, the most promising configuration will undergo static and dynamic testing to characterize its behaviour across relevant frequency and temperature ranges for a potential ESA application. Finally, a structural part prototype (e.g. supporting structure of a payload or structural bracket) incorporating NiTi SMA lattice structures will be fabricated and tested to demonstrate the advancements achieved through this integration.
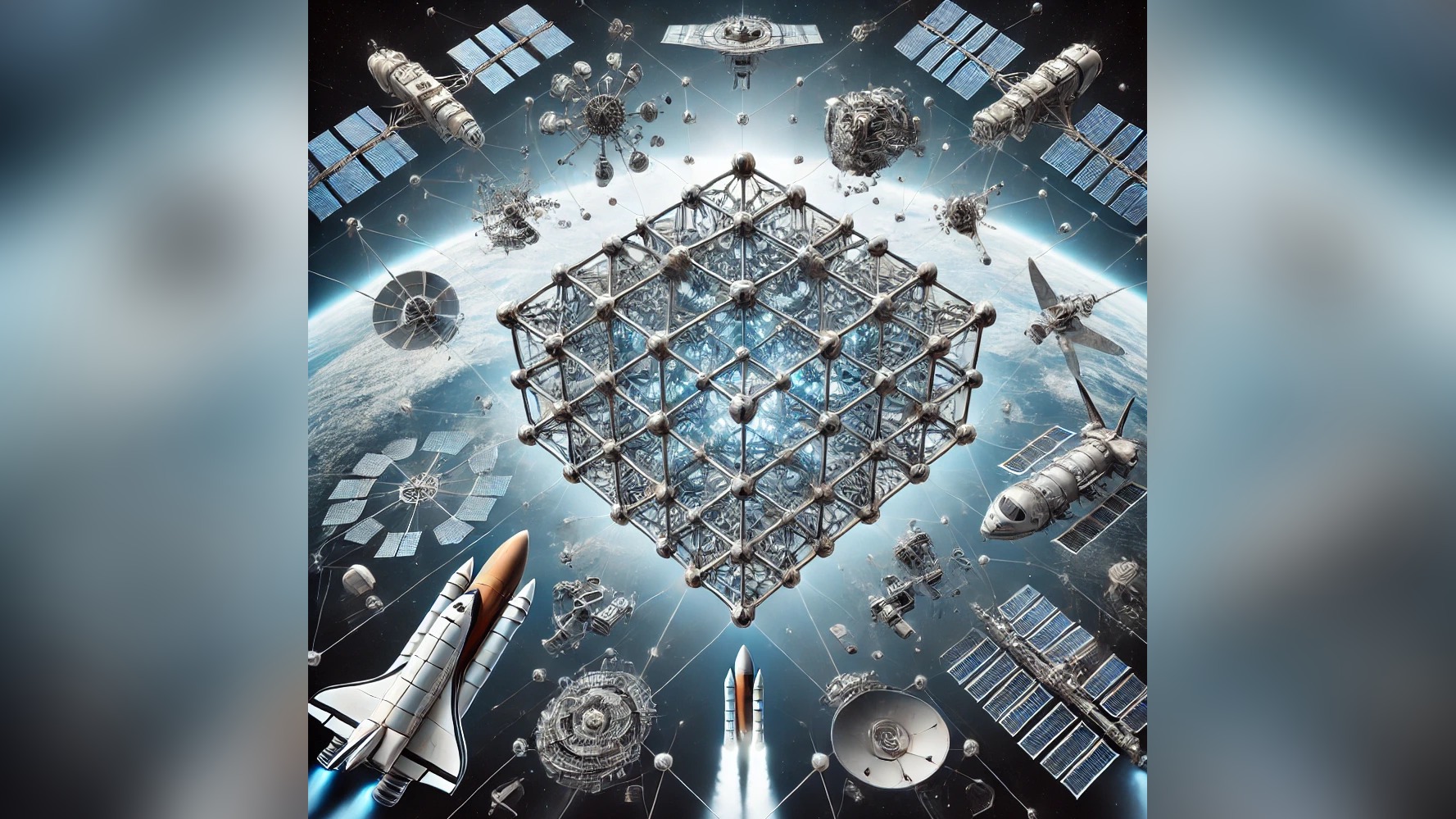