Duration: 18 months
This project proposes the development of a novel topology optimization methodology to continuous-fibre composite materials to design a CubeSat chassis structure, including experimental validation, expecting increases of 20% to 40% in stiffness and 25% in maximum load with respect to a composite baseline [1,2], and 60% mass reduction compared to a conventional metallic design [3], leading to unexplored design concepts and superior structural performances. This approach is expected to unlock the development of ultralight-weight structures for spacecraft systems. Recent research focuses on extending topology optimization from isotropic to directional composite materials to achieve even more lightweight structures. However, defining optimization procedures that consider maximum stress and material orientation in 2D remains a research challenge. State-of-the-art methods address these issues with simplified approaches that underutilize directionality or with computationally prohibiting features. Combining both aspects represents a significant advance in the state-of-the-art [4]–[7]. By extending novel stress-dependent topology optimization methods, introducing a design variable setting the orientation of directional materials in 3D space and proposing its local optimization with a gradient-based algorithm, this project will ensure the computational efficiency required to explore novel lightweight fibre-reinforced polymer structure designs. The design solution obtained will be experimentally tested, evaluating its structural integrity in conditions representative of the launching and operational environment. The proposed methodology can contribute significantly to reduce mass and fuel consumption of space and transportation systems, with a high potential for technology transfer aligned with strategic goals on environmental sustainability and economic growth across multiple sectors.
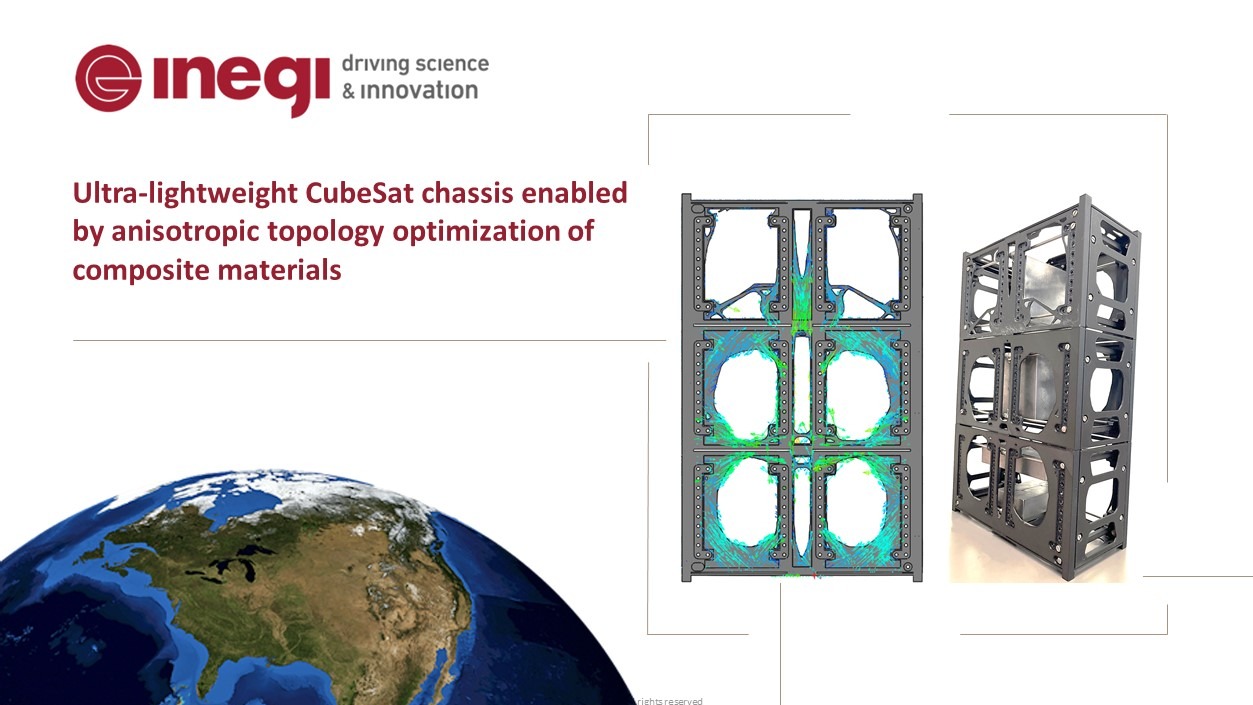