Duration: 36 months
Upcoming Moon exploration requires innovative approaches to equipment logistics, highlighting the significance of in-situ manufacturing. Leveraging local resources will be cost-effective and also align with sustainable practices, applicable to constructing radiation shields, landing pads and hardware components. Laser Powder Bed Fusion (LPBF), widely explored for terrestrial manufacturing due to its versatility and accuracy, has shown potential with lunar regolith simulants for in-situ manufacturing [1][2]. However, while LPBF achieves excellent geometrical accuracy with regolith simulants, its mechanical properties need improvement. Techniques like molten salt electrolysis [3] and carbothermal reduction [4], are used to extract oxygen[5] from regolith and obtain metallic or partially metallic materials which can be a suitable, high mechanical property feedstock for LPBF. LPBF of reduced regolith simulant obtained by molten salt electrolysis was investigated[6], with no conclusive demonstration. Indeed, one of the key challenges of regolith processing by LPBF, especially actual regolith, is the recoating of the powder bed, due to its irregular shape which hinders flowability. The proposed PhD aims to identify new successful solutions to use reduced/partially reduced regolith simulants as LPBF feedstock for in-situ manufacturing. To this aim, the PhD will define novel strategies involving a dedicated intelligent LPBF setup with integrated sensors to provide in-line data for modeling, optimizing and controlling the AM process (spreading and melting) via efficient Artificial Intelligence,Machine Learning. The PhD will specifically identify novel solutions for irregular powder spreading and melting to achieve first-time-right printing of defect-free component with enhanced mechanical properties. In addition, the proposed activity will investigate two regolith reduction processes, which will inform the achievable printed material properties for different reduction rates.
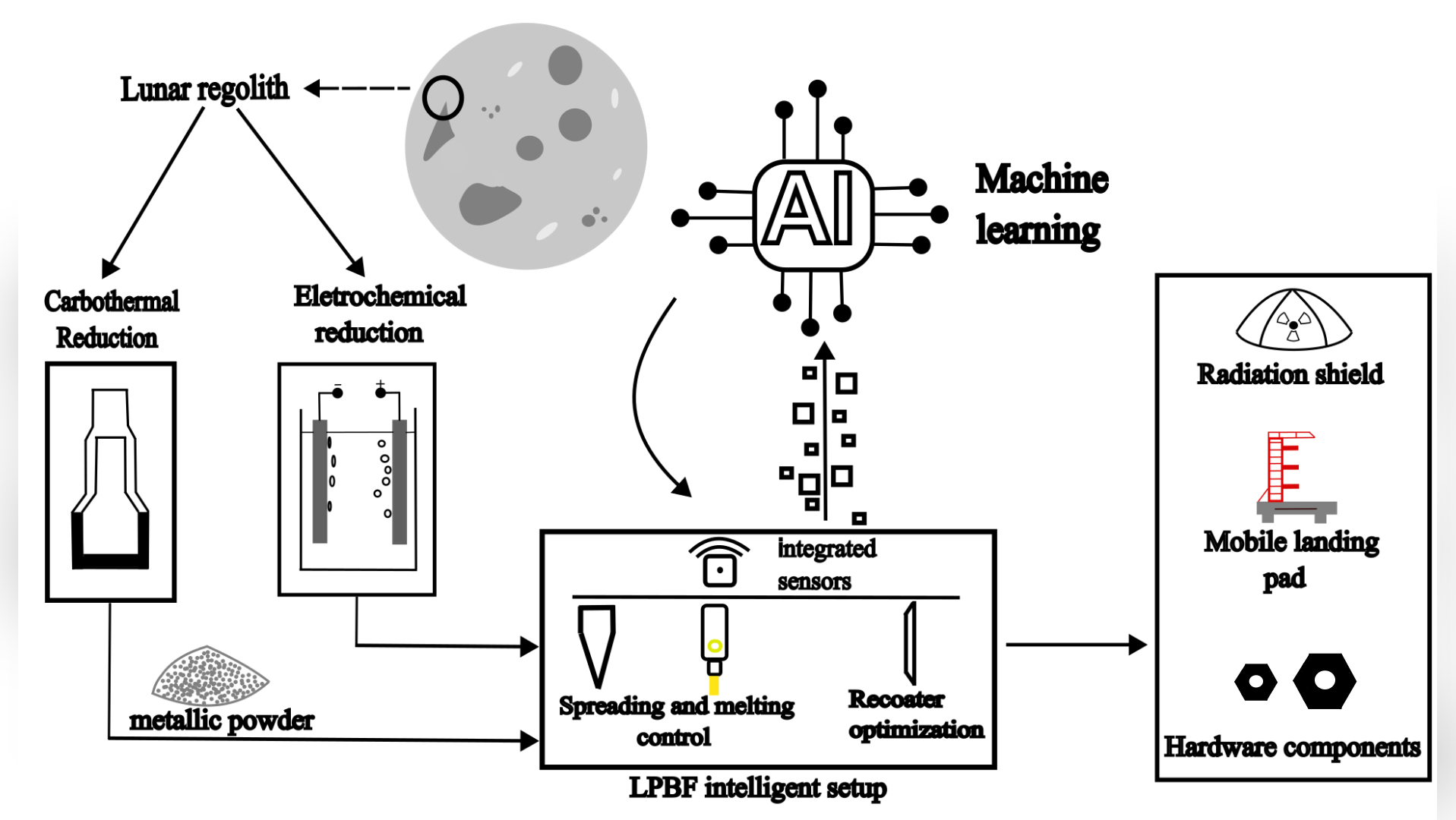