Duration: 36 months
The co-funded ESA project iAMinSpace (Contract No. 4000133882/21/NL/MH/ic) has shown the feasibility of using localized heat to debind and sinter Material Extrusion Additively Manufactured (MEAM) metal or ceramic parts, building the groundwork for in-space manufacturing of advanced space materials. This cost-effective method uses filaments embedded with metallic or ceramic powders, resulting in dense near-net shaped parts. The parts need to be first shaped, then debinded, and lastly sintered. A well-known disadvantage of the conventional method is the time consuming processing, being decoupled and often requiring toxic debinding agents. Our novel approach has shown that thermal debinding [1] and sintering [2] of MEAM parts can be achieved through an application of local energy by applying it selectively along the 3D volume of as-built parts. A low intensity laser and an induction heater were integrated in a hybrid MEAM system to enable in-situ debinding and sintering [3]. The results showed that the main binder can be removed, layer-by-layer, along the full volume via laser ablation of the organic mass [1, 3], with the sintered bodies reaching densities of up to 99.79% with very short sintering cycles [2]. Additionally, the system shows indications that multi-material metal-ceramic composites can be built [4]. In this follow-up OSIP project, an extension of multi-material printing will be conducted, investigating metal-ceramic composites (e.g., steel-zirconia, copper-alumina), as well as the dedicated processing parameters. The objectives include (O1) 3D printing of metal-ceramic composites and produce simple demonstrator parts; (O2) Investigate multi-material parts using pellets or pastes (as opposed to brittle filaments); (O3) Testing of printed parts (dimensions, visual defects), microscopy and composition (EDX/WDX, SEM/EBSD, CT), as well as mechanical (flexural & tensile tests). This technology offers an exciting route to produce advanced hardware in space.
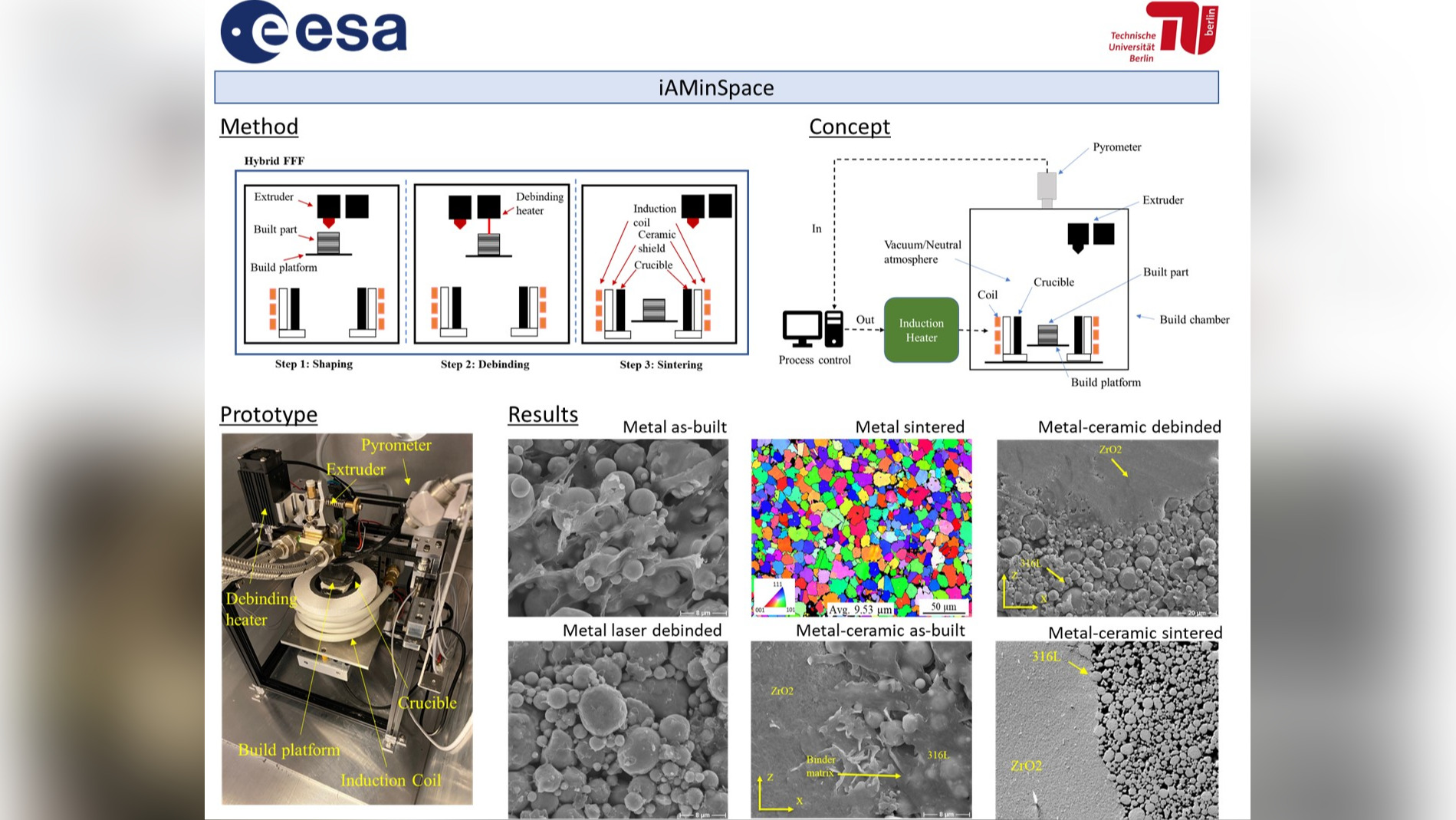