Fibre composites are widely used for space applications such as antennas, solar arrays and support structures because of their excellent mechanical properties, good thermal dimensional stability and strength to weight ratio. Currently the growth of composites as structural materials will depend upon the success of cost reduction which is now becoming the focus of attention for new developments. In the coming years, the space industry must assume the challenge of implementing additive manufacturing (AM) in an efficient way due to the need for lightweight parts, reducing cost and improving performance. Lately, an increasing demand for AM polymer composites with optimised mechanical properties is manifesting. Laser sintering (LS) has the potential to be of great importance in the development of reinforced polymers and is an AM technology that already meets the aerospace industry requirements. Previous research on reinforcements for LS focused on rather expensive nanoscale and microscale fibres but more cost-effective reinforcements are available and used on a broad scale in conventional manufacturing, i.e. glass fibre reinforcements. Glass beads (average size:57µm) are commercially used for LS powders as these can be homogeneously mixed in the powder. However, they are less efficient as these are shorter than the critical length required for complete stress transfer. For this project, this powder will be used as a benchmark for further exploration towards glass reinforced LS polymer parts with PA12 as matrix material. A comparison will be made with experimental LS chopped glass fibre (length:3-4mm, diameter:10µm) reinforced parts for which innovative powder/fibre deposition systems will be developed to be implemented in the LS machine. The results and experiences gained will be used to reach the principal objective; development of a proof-of-concept for LS continuous glass fibre reinforced parts with reinforcement in the z-direction, the weakest point of LS technology.
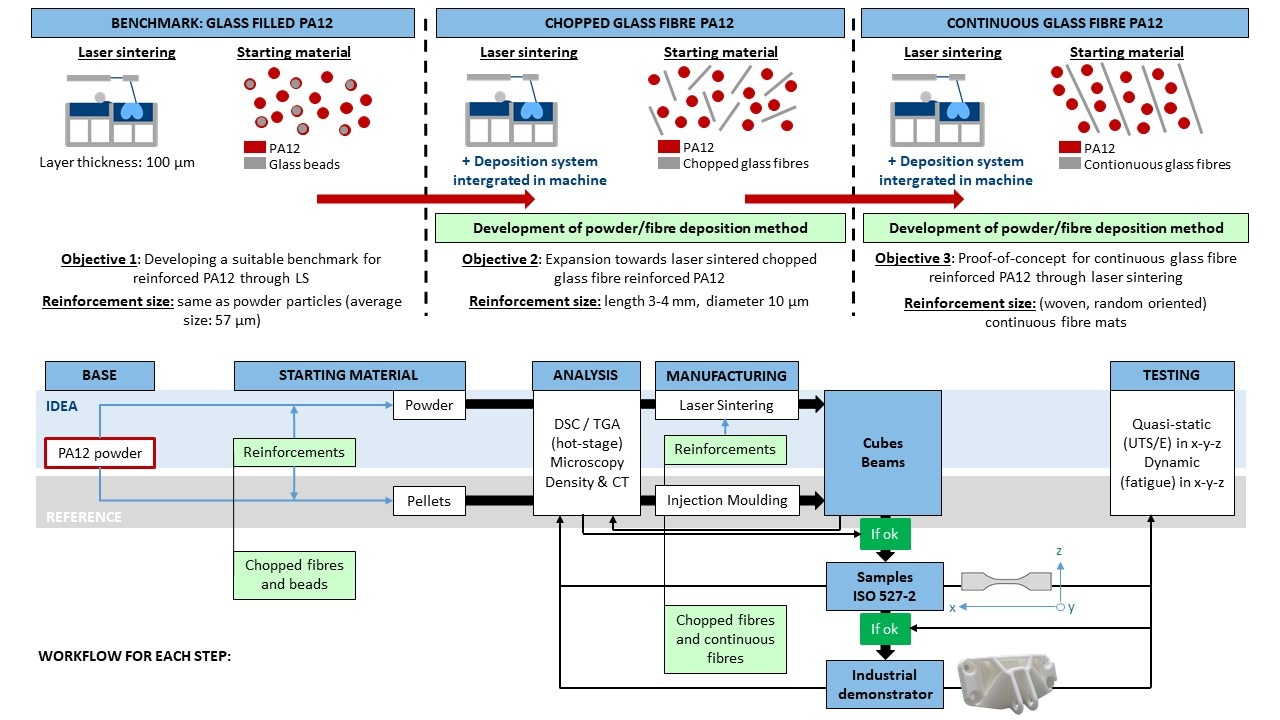