Reliable and efficient excavation and beneficiation of regolith will be the first necessary step for a future lunar ISRU process chain, and will be beneficial for exploratory and scientific activities. To address this requirement, a multi-disciplinary team at the University of Manchester is developing a novel excavation and beneficiation system that will be able to provide controlled feedstock to the successive analytical and ISRU processes. Granular size separation is a key requirement of many ISRU applications, yet the proposed combination of these two operations into a single system is a novel concept that has not been realised in previous work. Low excavation forces are crucial for systems operating in the lunar environment, as early ISRU missions will utilise small robotic vehicles with limited available drawbar force. Thus, continuous excavation processes are preferable to discrete methods, where augers are an interesting alternative to bucket wheels due to their simplicity and the extensive terrestrial use of augers to transport abrasive and cohesive granular materials. Therefore, the proposed system utilises a single (flexible) auger for excavation, material transport, and facilitation of size separation in a shearing sieve, thus combining three mechanisms in one system. To mitigate issues associated with auger systems, the system will utilise a specifically designed inlet that both rejects coarse particles and guides regolith towards the auger. Previous work focused on pushing material with blades, whereas the proposed activity focuses on geometries that lift material off the surface and guide it towards the auger while maintaining low excavation forces. During development, wear of the inlet structure caused by the constant interaction with the abrasive regolith will be investigated. The project is timely given ESA’s newly developed Space Resources Strategy, and will fill technical knowledge gaps around excavation, beneficiation, and feedstock refinement.
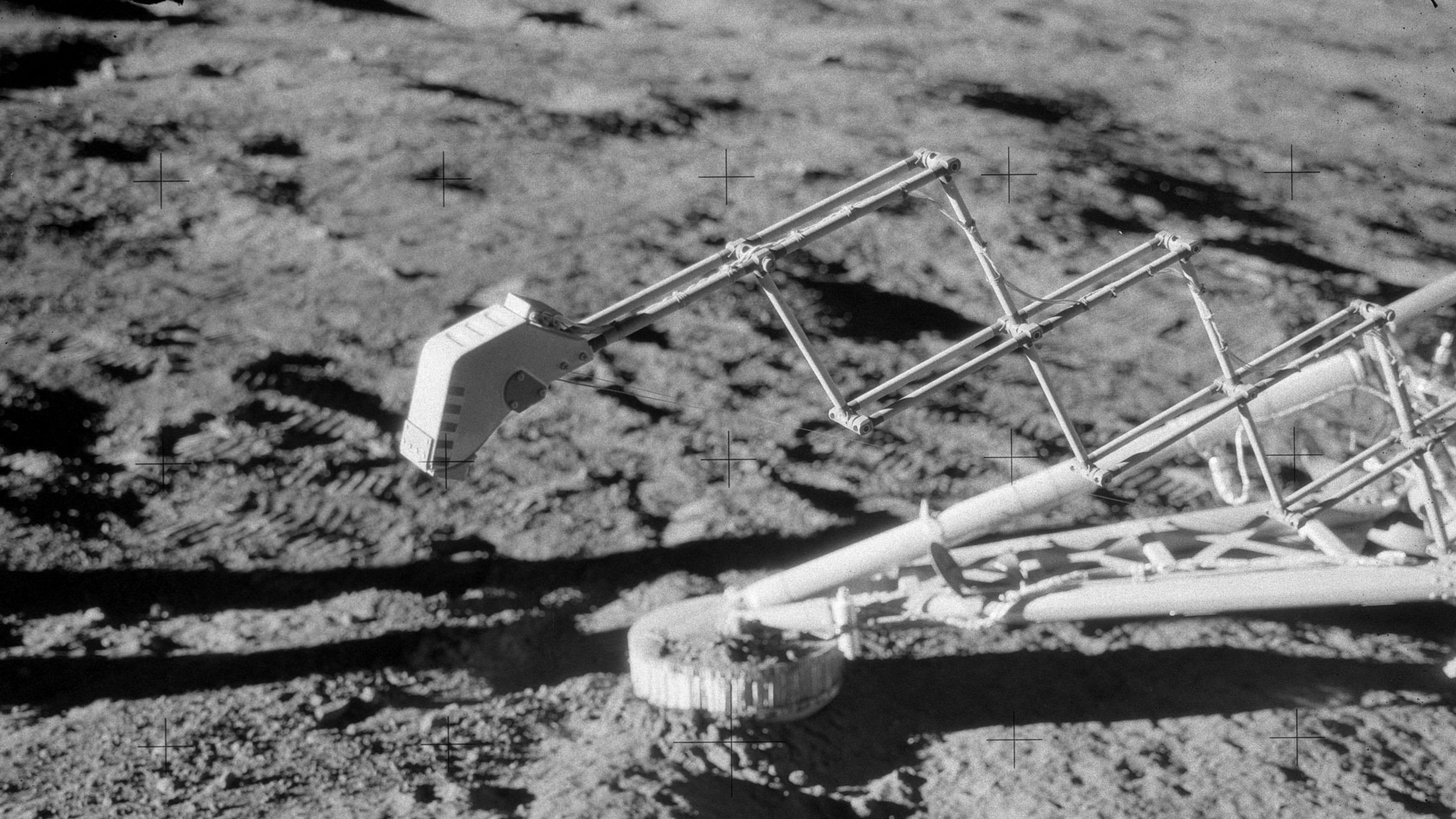