One of the main trends for long space mission is the implementation of a whole new maintenance strategy allowing on-demand manufacturing, on site, of spare parts for onboard equipment replacement. The idea for this proposal is: if we can print spare parts in microgravity using advanced thermoplastics, can we also manufacture energy sources such as lithium ion batteries (LiB)? Would it be possible for astronauts to 3D print on-demand, replacement LiB of various formats to power onboard equipment? Through the MELT Project, a fused filament fabrication (FFF) 3D printer capable to meet microgravity operational constrain was developed to print PEEK based mechanical spare parts and is suitable to process any thermoplastics and their composite (loaded Filaments). Recently we have demonstrated that it is possible to fabricate composite polymer filaments for FFF 3D printers that are highly loaded with active materials and can be used to print complete functional LiB. Their ongoing studies also demonstrate the impact of printing parameters on charge distribution (sedimentation effect) in the 3D-P batteries and on their electrochemical performances. Sedimentation phenomenon occurs because of the Earth's gravitation. What would happen in microgravity? By Combining the Know-How and skills of ESA-ESTEC and LRCS, we propose to first simulate the effect of microgravity on 3D-P batteries using the MELT printer. We will study the charge distribution, the quality of the interface and the electrochemical performances of the 3D-P batteries using an arsenal of techniques available in our laboratories. Based on these findings we will adapt the filament formulations to propose a kit of stable and inert composite feed stock materials (FSM) in the form of filaments that can be transported, stored for a long period of time. These FSM can be used out-of-earth (as initial target on board the ISS) in order to 3D print the first full lithium-ion battery in microgravity.
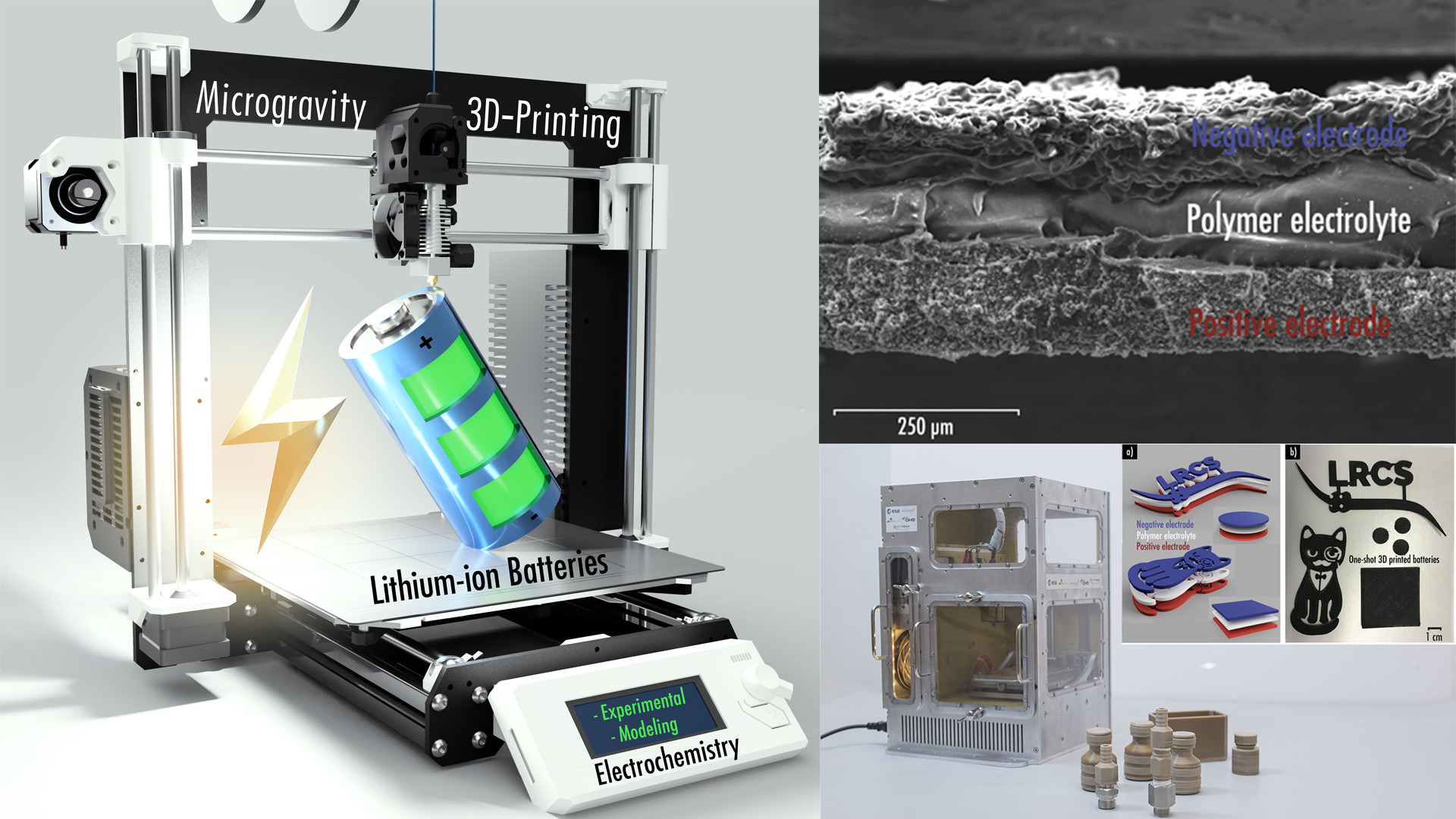