Duration: 18 months
While widely successful, additive manufacturing (AM) of metal has a major challenge in succesfully adopting high-strength aluminum alloys, where the strengthening elements (Cu or Zn) also cause cracking through a mechanism called hot tearing, where narrow but extended melt networks form, and as the network eventually solidify and shrink, microstructural residual stresses hot spots form, eventually leading to microcracks which render the solidified material unusable. Despite the importance of this issue, we are not aware of physically sound dendrite-level models that explicitly simulate microstructural residual stresses or hot tearing in AM, allowing for quantitative assessment of AM printability. In this project, we will develop a simulation framework to assess printability of high-strength aluminum alloys. We implement a quantitative rapid solidification phase field model (PFM) to explicitly resolve the dendritic solidification, microsegregation, and competitive grain growth; this PFM is then coupled to crystal plasticity (CP) to capture solidification shrinkage stresses and solid-state thermal contraction. When these microstructural (type II-III) residual stresses lead to sufficiently large plastic deformation, ductile cracking is expected, which we model with Rice-Tracey or anisotropic continuum damage methods. This framework is implemented using a high-quality open-source software library, MOOSE. Input temperature data is taken from a melt pool model developed elsewhere. For validation, we will prepare single scan laser tracks of relevant high-strength aluminum alloys: Scalmalloy and 2xxx or 7xxx series alloys. Then we characterize their texture, grain morphologies and grain boundary statistics with EBSD; microsegregation with EDX; and the microcracks will be identified in relation to key microstructural features, and compared to the simulations. This simulation framework will serve as a tool to quantitatively assess printability of modern high-strength alloys.
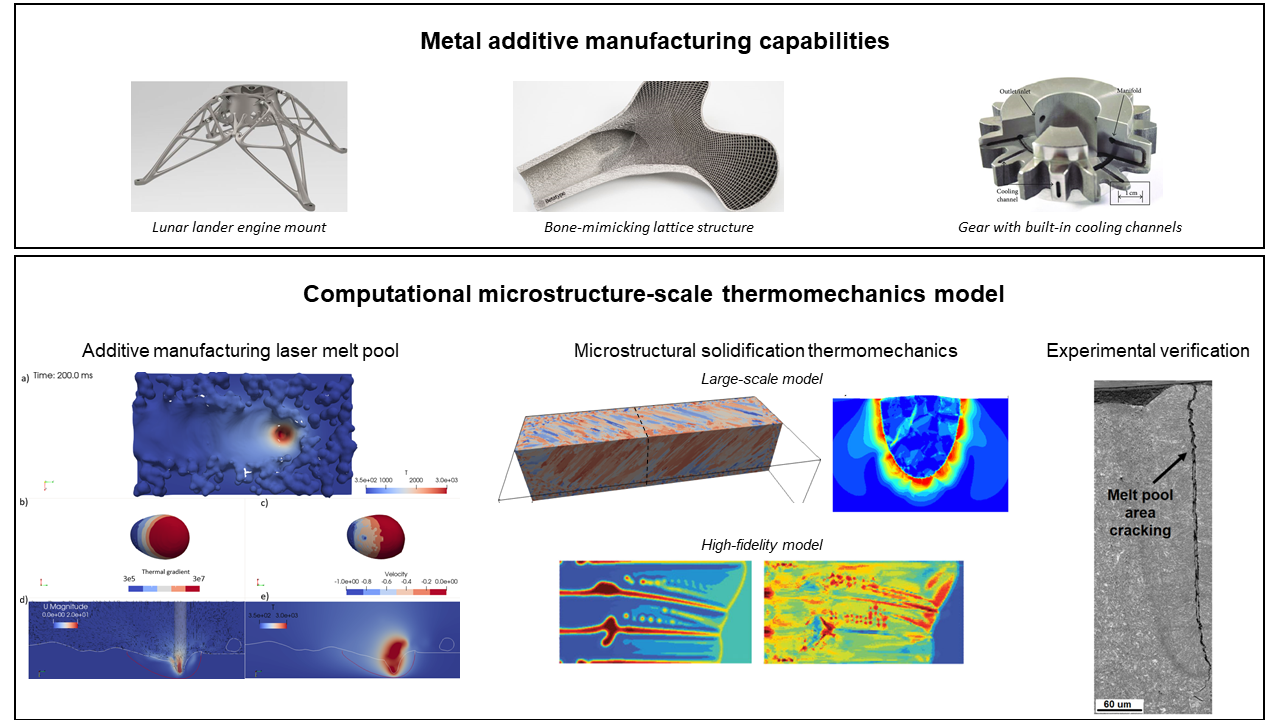