
Closed
Here, the unique design flexibility of Powder Bed Fusion (PBF) has been applied to manufacture, mechanically test, and analyse, auxetic cubic chiral lattice structures. This lattice structure is a perfect candidate for habitat outer shells due to its synclastic bending behaviour and high energy absorption capabilities.
Laser Powder Bed Fusion (L-PBF) has received increasing attention being a reliable technology suitable for ISRU. However, obtaining the optimal parameters to AM rich oxidised metals, such as fine lunar grey soil β Regolith, requires extensive characterisation and understanding of the sintering/melting and solidification mechanisms.
Here, a preparatory study based on a combination of synchrotron in situ x-ray imaging and post operando techniques, gives insights on the effect of solid and liquid oxidation phenomenon. The oxygen species acting as a surfactant, reverses the Marangoni flow, deepening the molten pool and assisting pores escape, whilst acting as an Ξ± stabiliser, improves the Ti alloy microstructure.
Printability tests campaigns followed on two lunar Regolith simulants with different mineralogy. A comprehensive simulants characterisation highlights different thermophysical properties (e.g., optical, melting, spreadability) driving activities to formulate an internationally accepted classification. For the first time, synchrotron in situ x-ray experiments have been used to image real time laser interaction, melt flow dynamics and solidification mechanisms of Lunar Regolith simulants. The change of molten pool morphology with process parameters (e.g., depth, width) has been quantified and the process instability mechanisms, that dominate the process under non optimal conditions (e.g., vapourisation, balling and sputtering) have been evidenced.
All that is instrumental to validate multiphysics models of laser sintering/melting of Regolith under Moon-representative environmental conditions and to identify novel printing strategies and chemically adapted Regolith powders to improve the mechanical performance of geometrically complex architectures.
This research project provides insights into the utilisation of laser additive manufacturing for ISRU applications. The ultimate goal is to use L-PBF technology and Regolith powder to fabricate the lattice structure for the lunar outer dome.
In the first part, a lattice topology that exhibits auxetic properties, high energy absorption capacity and conforms to synclastic (dome-shaped) curvatures under out of plane bending stress is presented as an ideal choice for applications necessitating curved components such as the protective outer dome in lunar habitats. Combing FE and experimental data, the compressive performance of an auxetic cubic chiral lattice was evaluated, leading to the following conclusions:
- The elastic-plastic performance of an auxetic cubic chiral lattice follows a bending dominated scaling law. The compressive response consists of a linear regime followed by plateau stress and densification.
- In the linear regime, the auxetic response is isotropic and with πππ=β0.32.
- In the plastic regime, the auxetic capability decreases with relative density, i.e., the strutsβ slenderness ratio, and reveals preferred contraction directions.
- The FEA shows that in a defect free lattice, plastic hinges on vertical struts are the dominant failure mechanism. However, the experimental tests reveal that struts with reduced cross-sectional area dictate failure locations.
- The ductile failure criterion defined in the FE model can predict deformation and initiation of ductile failure with good accuracy.
This feasibility study explored the potential use of lightweight auxetic lattice structures for the outer dome of lunar habitats. It also showcased the value of FEA in the design process and the impact of manufacturing defects, such as pores and dimensional variations, on the mechanical performance.
This study then focuses on the design of laser additive manufacturing strategies tailored for challenging particulate materials, specifically those composed of highly oxidised metals like lunar Regolith simulant powders. The use of advanced in situ inspection technologies has facilitated a deeper comprehension of critical laser-matter interactions.
The first set of experiments investigated the effects of high oxygen on Ti alloy powder, as this scenario may occur when utilising poorly refined metals on the Moon. This study, using in situ synchrotron x-ray imaging found:
- Oxygen species reverse the Marangoni force, inducing a centripetal metal flow that deepens the melt pool, and aids in the escape of the pores, dragging them away from the solidification front.
- The presence of oxygen promotes the formation of a tetra modal πΌ phase microstructure in Ti6242, raising the πΌ to π½ transus temperature. This microstructure has been reported to have superior fracture toughness performance, attributed to the πΌπ phase deflecting the propagation of cracks [222].
- The formation of oxides, shifting from Ti (rutile) to oxides primarily composed of Si and Zr oxides, alters the properties of the oxide scale, enhancing Ti6242 oxidation resistance.
These insights into the oxidation phenomena during L-AM of Ti6242 helped define practices for improving the manufacturing stability and controlling the resultant microstructure and defect formations.
This study continues with a comprehensive experimental campaign on printing lunar Regolith simulant powder. A comprehensive characterisation of two lunar Mare Regolith simulants, the European Astronaut Centre lunar Regolith simulant (EAC) from ESA and the commercially available lunar mare simulant (LMS) from Exolith Lab ltd, reveals that:
- At the laser wavelength (π=1064 nm), the diffuse reflectance of EAC powder is ~30% and 8% higher than the diffuse reflectance of LMS powder. This difference might be due to the 25wt% higher Olivine concentration and anorthosite presence in EAC.
- EAC and LMS powders have a shear thinning behaviour, as the angle of repose decreases with rotational speed. LMS powder reaches high flowability properties, i.e., very-free flow, at 60 rpm. At low rotating speed, EAC powder has a 17% higher cohesive index resulting with poor spreadability properties.
- Small differences in melting and glass transition temperature are observable. LMS powder has a melting temperature of 1280 Β°C, that is 4.6% higher than the melting temperature of EAC. This might be
due to the higher concentration of high melting temperatures oxides such as MgO and CaO.
These insightful findings, on the powder properties relevant for L-AM, have the potential to guide the development of globally recognised and standardised classification schemes for lunar Regolith simulant materials.
In the final part of the study, a printing campaign was conducted on an industrial L-PBF machine, to the delineate the process map. Then, in situ synchrotron x-ray imaging experiments were conducted to observe the laser-matter interaction varying the process parameters. A combination of in situ and post operando analysis reveals that:
- By fluctuating laser power, scan speed and hatching space, five different build categories were delineated as: (i) no deposition; (ii) not consolidated β balling effect; (iii) consolidated β sintering; (iv) consolidated β vitrification; and (v) not consolidated β vaporisation. The processability window for obtaining consolidated sintered samples was found to be very narrow.
- Al6062 substrates demonstrated to successfully bond with lunar Regolith simulant powders; while fused silica and refractory clay substrates failed.
- The rescan strategy was demonstrated to improve sample consolidation and increase print volume.
- It is hypothesised that because of the higher melting temperature and laser reflectivity of EAC, the temperature reached at (iii) consolidated β sintering conditions for LMS powder, is insufficient for homogenous substrate/powder wetting. The highly viscous melt pool solidifies fast enough to create isolated beads, and hence, a discontinuous track.
- Excessive laser energy density causes a deep penetration of recoil pressure into the substrate causing the formation of keyhole pores. From in situ observation, the trajectory of both hydrogen and keyhole pores follows an inward, i.e., reversed, metal flow.
- Excessive laser energy density on samples made of pure lunar Regolith simulant causes liquid spattering as a combined effect of Marangoni driven flow and recoil pressure. It is hypothesised that the major contributor of surface tension, SiO2, reduces the surface tension of the melt pool [254] meaning a lower kinetic energy threshold for the droplets to escape.
- In situ experiments allowed the calculation of pure Regolith simulant melt pool geometry variations with process parameters.
- Cylindrical samples with 53% porosity, were mechanically tested and exhibited a compressive streght value of 6.2 MPa which is comparable to that of masonry bricks. When Regolith simulant powder is mixed with 10wt% of AlSi10Mg powder, the resulting strength value is 5.8 MPa accompanied by a 75% increase in strain, leading to an overall improvement in ductility.
These results help identify practices for optimising additively manufacturing Regolith components on earth starting from the particulate state. Variations in powder properties have been identified and their potential influences on the manufacturing process window are discussed. It becomes imperative to establish manufacturing processability windows tailored to specific mineralogical compositions within distinct lunar geographical regions. In addition, the first in situ synchrotron x-ray imaging experiment was conducted to observe the laser melting of lunar Regolith simulant. These data can be used for validating multiphysics models aimed at replicating the laser melting under real lunar environment conditions.
Although this research represents the initial phase of validating L-AM processes for large-scale part manufacturing, it provides valuable insights into the potential for designing a feasible and sustainable printing system for ISRU applications.
Systems for launch and space vehicles are currently assembled from a multitude of components and subsystems. Direct fabrication of entire (sub)systems as a single component would be transformational in reducing the number of manufacturing systems required in space, and hence payload. Additive manufacturing (AM) enables unprecedented design freedom and topologically optimisation, enabling the fabrication of previously undreamt-of shapes. However, most AM techniques are currently limited to a single material, still requiring multiple components to be assembled. Using innovative techniques calibrated using synchrotron imaging, University College London will develop methods of additive manufacturing graded materials, enabling a range of functional and structural properties in one component. An example would be a heat shield with a refractory surface transitioning into a high thermal conductivity material. Another example would be direct printing of lunar habitat structures that has thin reflective metallic air-barriers transitioning into insulating structural honeycombs fabricated from local regolith. Using a unique AM machine that works on a synchrotron beamline, the conditions for forming functionally graded composites from nano-structures to whole components can be investigated. Using terrestrial synchrotron imaging we can determine the optimum conditions required to additive manufacture graded at a nano-scale up to the component scale, through hierarchical lattice structures. The project is timely as ESA has highlighted Additive Manufacturing as a key novel technology for production of components both terrestrially, on the International Space Station, and for production of Lunar Habitats using local resource. This project will fill technological gaps in predicting the service performance of components fabricated using this innovative technology, contributing to the development of systems that have increased functionality at a lower cost, with known properties.
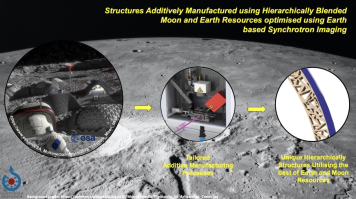